
Why 3/4-inch check valves? Uncover the secret weapon of air compression systems
In this section, we will explore why 3/4-inch check valves have become the first choice for many engineers and technicians. From basic functions to complex application case studies, it reveals how this valve stands out in a variety of environments, ensuring that the air compression system is always in the best condition. By comparing different sizes and other types of valves, its advantages are further highlighted.
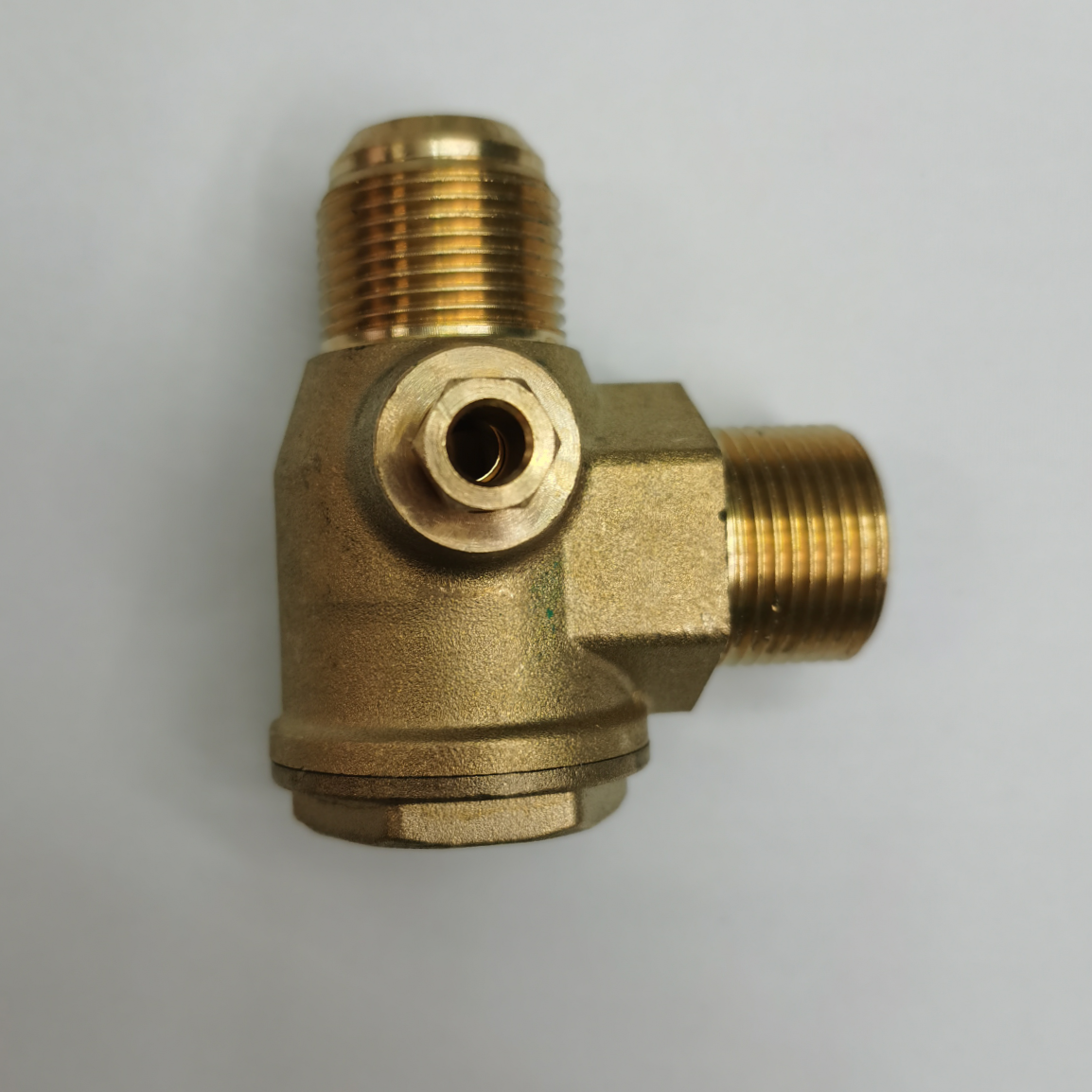
Whether in a factory workshop or on a construction site, the air compression system is an indispensable part. Which play a key role is the check valve. Especially for the requirements of high flow and high pressure difference, 3/4 inch size check valve with its compact design and efficient performance is the ideal choice. Compared with other sizes, it can ensure sufficient circulation area and will not take up too much space; compared with ordinary gate type or butterfly valve, it has a faster and more sensitive response speed and better sealing effect.
Full analysis of working principle: in-depth understanding of internal structure and operation mechanism
In order for the reader to better understand the function of the 3/4 inch check valve, its structure and operation will be explained in detail here. Including the specific location of the main components such as springs, seals, etc. and their tasks; and explain how these components work together to achieve one-way flow control when the pressure changes. Some common failure modes and preventive measures are also mentioned.
The core of the 3/4-inch check valve is a set of well-designed mechanical structures. The inlet end is equipped with a light but durable stainless steel sphere as the switch mechanism, which is matched with a soft seat cushion made of special rubber to form a tight closed surface; the outlet side is equipped with a pressure spring with strong reset force but not excessive tension to maintain Normal opening posture. Once there is any abnormal pressure drop trend in the reverse direction, the sphere will immediately be pulled by its own gravity and automatically fall back into place to block the channel opening, thus preventing the occurrence of medium backflow. This simple and ingenious design not only improves the reliability of the work but also reduces the maintenance cost.
Installation Guide: Easy Steps to Get Started Quickly
Even operators without much experience can follow simple instructions to complete the correct installation process. This article walks the user step-by-step through the list of tools and materials needed, and provides a detailed graphic tutorial on what needs to be noted at each stage. Emphasis is placed on the importance of correct positioning and smooth connection to avoid potential problems.
firstly, it is necessary to prepare appropriate wrench and screwdriver for tightening the nut and fixing bracket; secondly, make sure that all interfaces have been coated with appropriate amount of lubricating oil to avoid dry friction and damage to parts. Then carefully place the new check valve into the predetermined hole and align it with the positioning pins on the flanges on both sides for preliminary alignment correction. A special jig is then used to assist in the application of uniform torque until the specified value is reached. Finally, it is necessary to carefully review whether all the assembly links are firm and reliable before putting them into use.
Daily Maintenance Secrets: Tips for Increasing Life and Increasing Efficiency
Regular inspection and proper maintenance can not only extend the service life of the product, but also improve the overall work efficiency. Here we have listed a series of easy-to-implement but vital recommendations-from cleaning surface dirt to replacing aging parts to lubricating moving parts and more. Each step helps maintain good performance and reduce the risk of unplanned downtime.
Arrange appearance inspection at least once a week to remove dust and impurities in time to prevent the heat dissipation and ventilation path from affecting the temperature adjustment ability. Every month, take time off to remove and clean the filter core and re-inject fresh hydraulic oil to ensure smooth transmission without blocking interference. About half a year, depending on the specific situation, consider updating a batch of vulnerable consumables such as O-rings and other sealant strips, which can greatly reduce the probability of leakage hazards caused by wear and tear. In addition, a comprehensive in-depth overhaul is carried out every year to evaluate the overall health status and make targeted improvement plans.
Real Feedback Collection: Listen to what users say
Collect comments from professionals from all walks of life on this type of check valve. What challenges do they encounter in practice and how do they solve these problems? By sharing stories with multiple customers, we can learn more about the actual performance of the product in the field, so as to provide more reference information for purchasing decisions.
Mr. Li, who works in the chemical industry, said: "Since the replacement of these new models, I have never been fined for gas leakage." It turns out that the poor sealing performance of the old style often causes trace toxic volatiles to escape and pollute the environment, causing dissatisfaction among the regulatory authorities. "Now the quality of this new brand really has no words!" He sighed from the bottom of his heart. Another master Wang also praised in the maintenance class of the hydropower station: "in the past, the small iron pieces were especially easy to rust and get stuck. it took half a day to pry open and clean them every time. However, after I bought it this time, I found that I didn't have to worry about this happening any more." It can be seen that good product quality and service can really make users feel satisfied and assured.
Safety Barrier Beyond Expectations: A Sharp Way to Ensure Production Continuity
The final discussion is one of the core values of this 3/4-inch check valve in the industrial field-safety protection. It can prevent harmful substances from leaking or flowing back into the pipeline network to cause greater losses in an emergency. The article will illustrate the story of how relying on such a small device saved the entire production line and even the safety of life and property in several typical accident cases.
a large iron and steel plant once suffered a serious interruption of cooling water circulation. at that time, if it had not relied on the excellent performance of several 3/4 inch check valves on site to successfully cut off the risk of secondary damage caused by the impact of water flow in the reverse direction, the consequences would have been unimaginable. Afterwards, the person in charge said with emotion: "Fortunately, there are such reliable equipment guarding our facilities! Otherwise, I really don't know what bad things will happen." Many companies have experienced similar experiences, and such little heroes are always indispensable at critical moments.
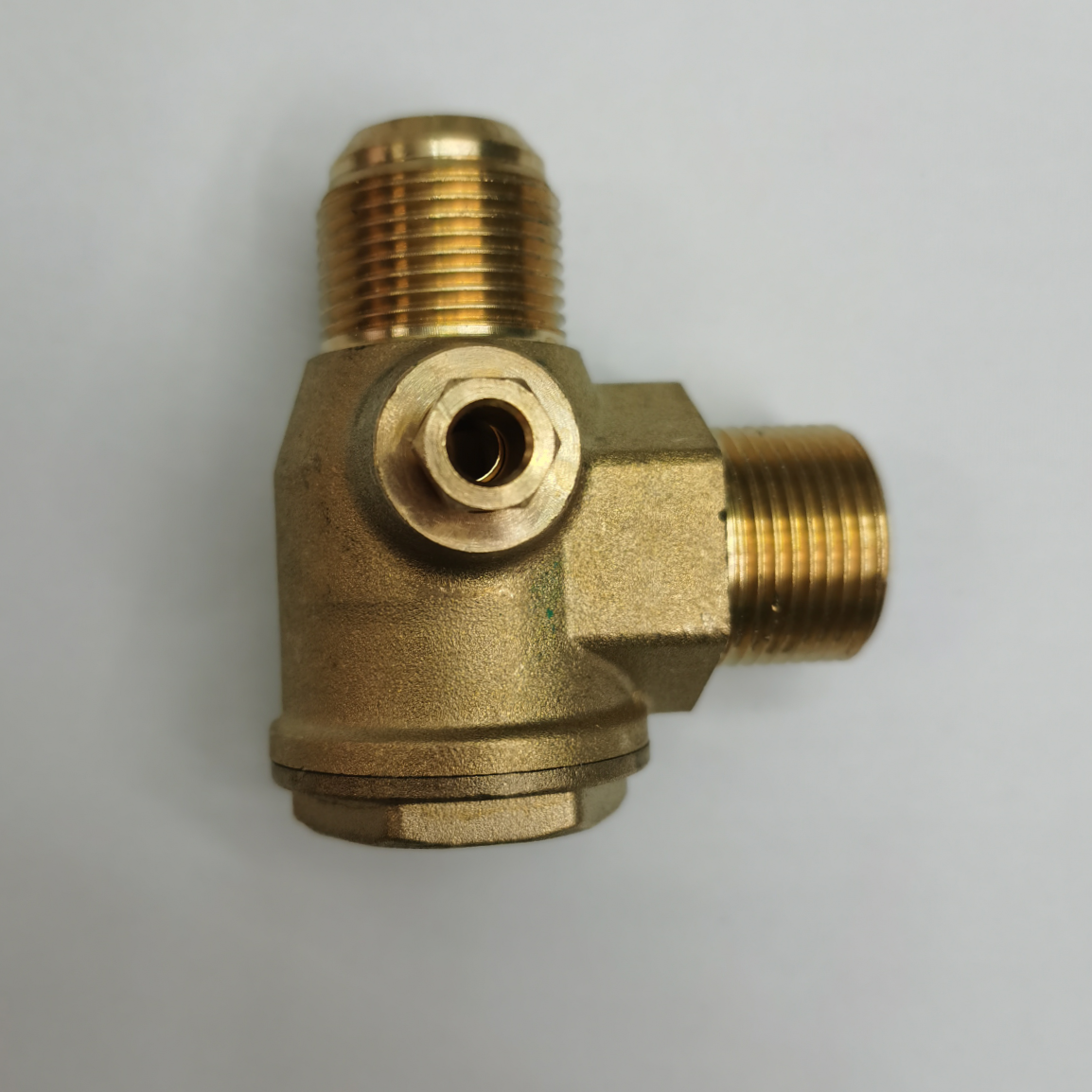