
Air Compressor Required:
3/4 inch Check Valve Purchase and Application Complete Solution
The secret of the 3/4-inch check valve: why it is an indispensable part of the air compressor
First, we will reveal why the 3/4-inch check valve plays such an important role in the air compression system. Understand its core functions-that is, to prevent gas backflow, ensure pipeline pressure stability, and improve the efficiency of the overall system. Through the study of industrial application examples, the reader can see how the component directly affects the safety and reliability of the production process.
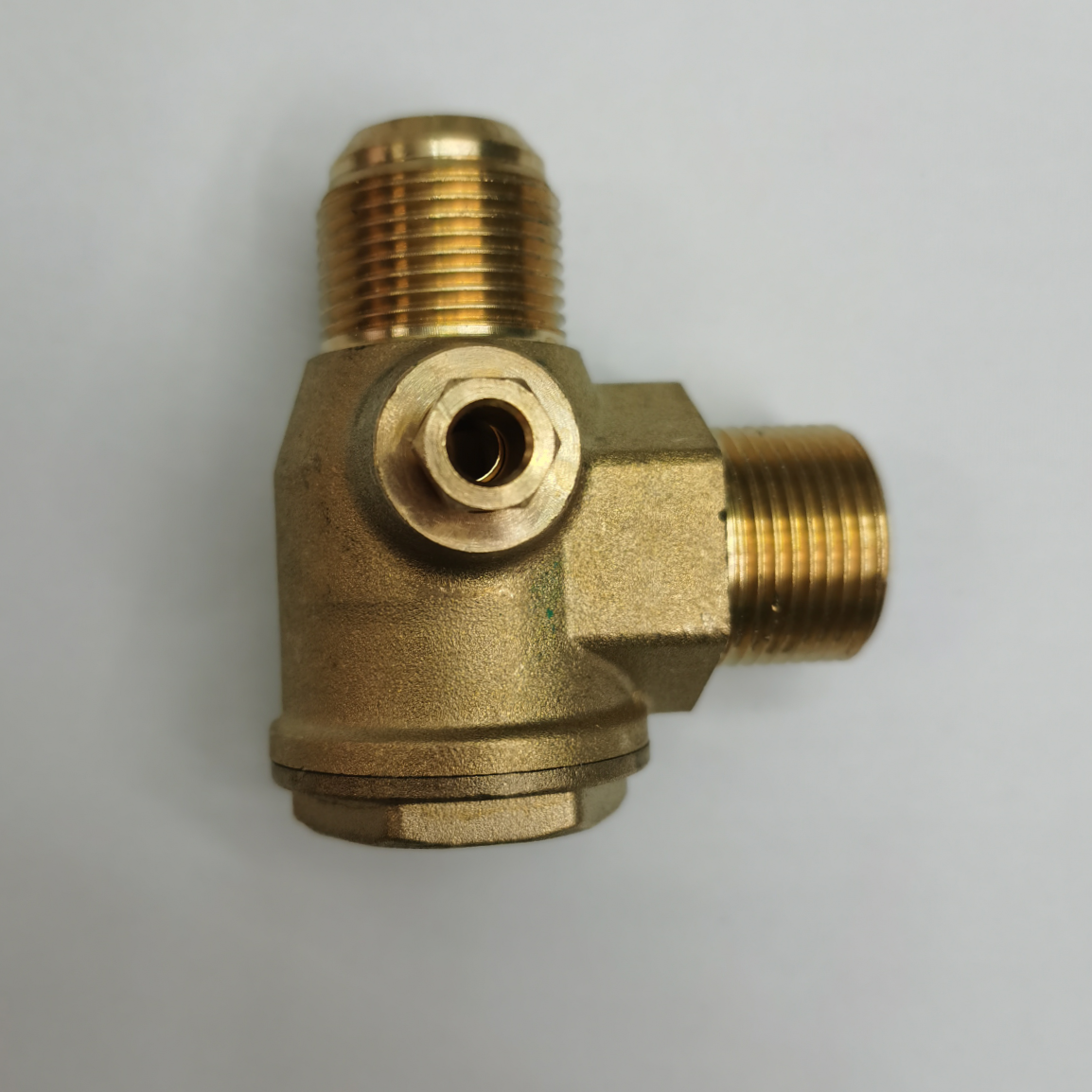
As one of the key components, the presence of the check valve ensures that the air compressor can operate normally under high pressure without leakage or backflow. This is especially important for businesses that rely on precise control of air quality, as it not only reduces downtime, but also greatly reduces the risk of loss due to accidents.
Behind the Science: How to Operate to Ensure Optimal Performance
Next, we will discuss the technical details of the check valve, including its internal structure and working mechanism. Explain the process of valve closing and opening, and analyze the contribution of different materials to durability and sealing. This section is designed to give technicians a better understanding of the complex engineering behind this small part.
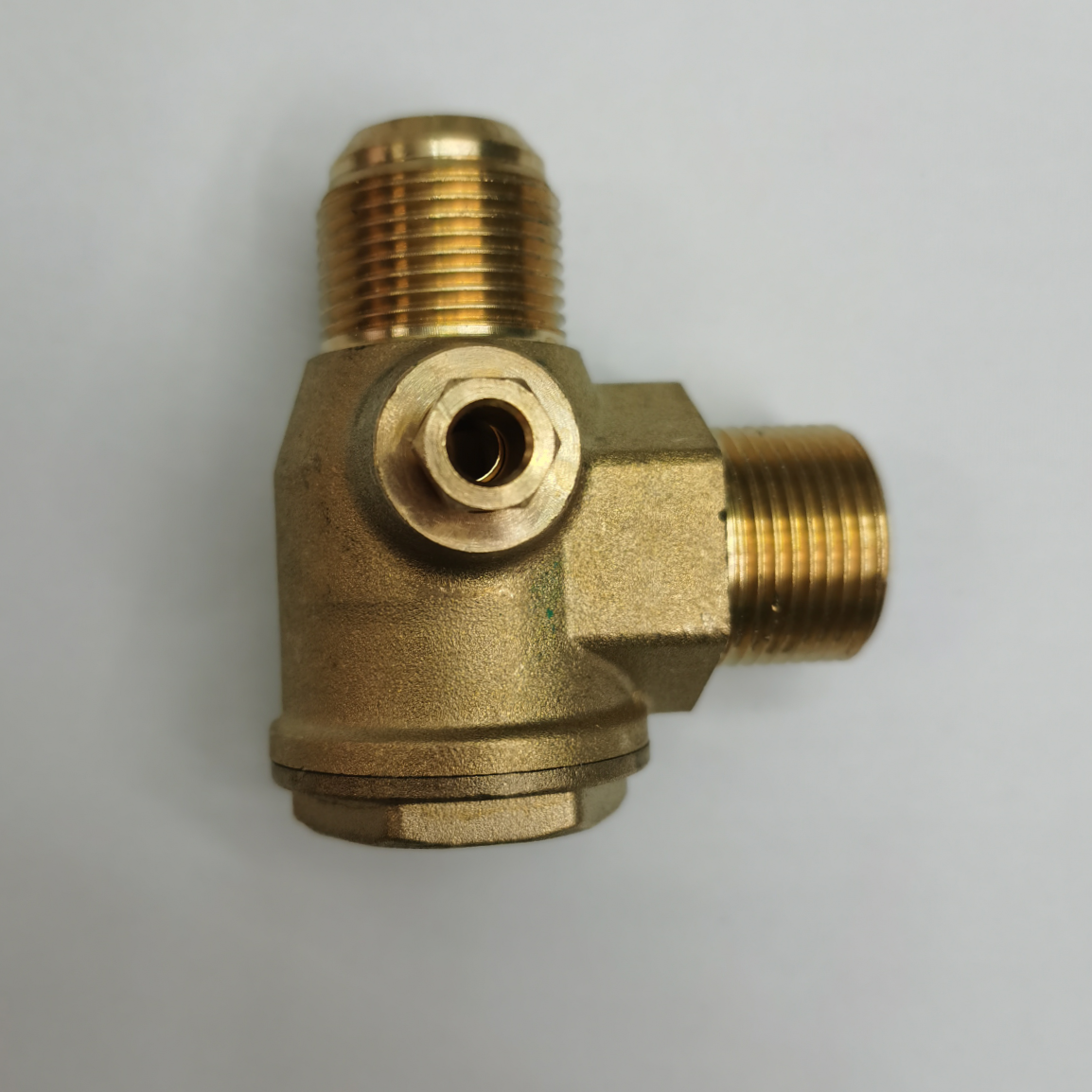
The choice of high-quality materials is an important factor in determining the performance of the check valve. Metals such as cast iron, stainless steel and brass have excellent corrosion resistance and strength, while rubber provides excellent sealing results. Through reasonable combination and collocation, an ideal product that is both strong and durable and can remain tightly closed for a long time can be manufactured.
Choosing the right size and parameters: the selection guide helps to make informed decisions
With the many brands and models on the market, how can you choose the product that best suits your needs? This section provides a detailed selection guide covering flow requirements, maximum allowable differential pressure, and other key metrics. The advantages and disadvantages of each style are presented in the form of comparison charts, so that users can make rational judgments according to specific working conditions.
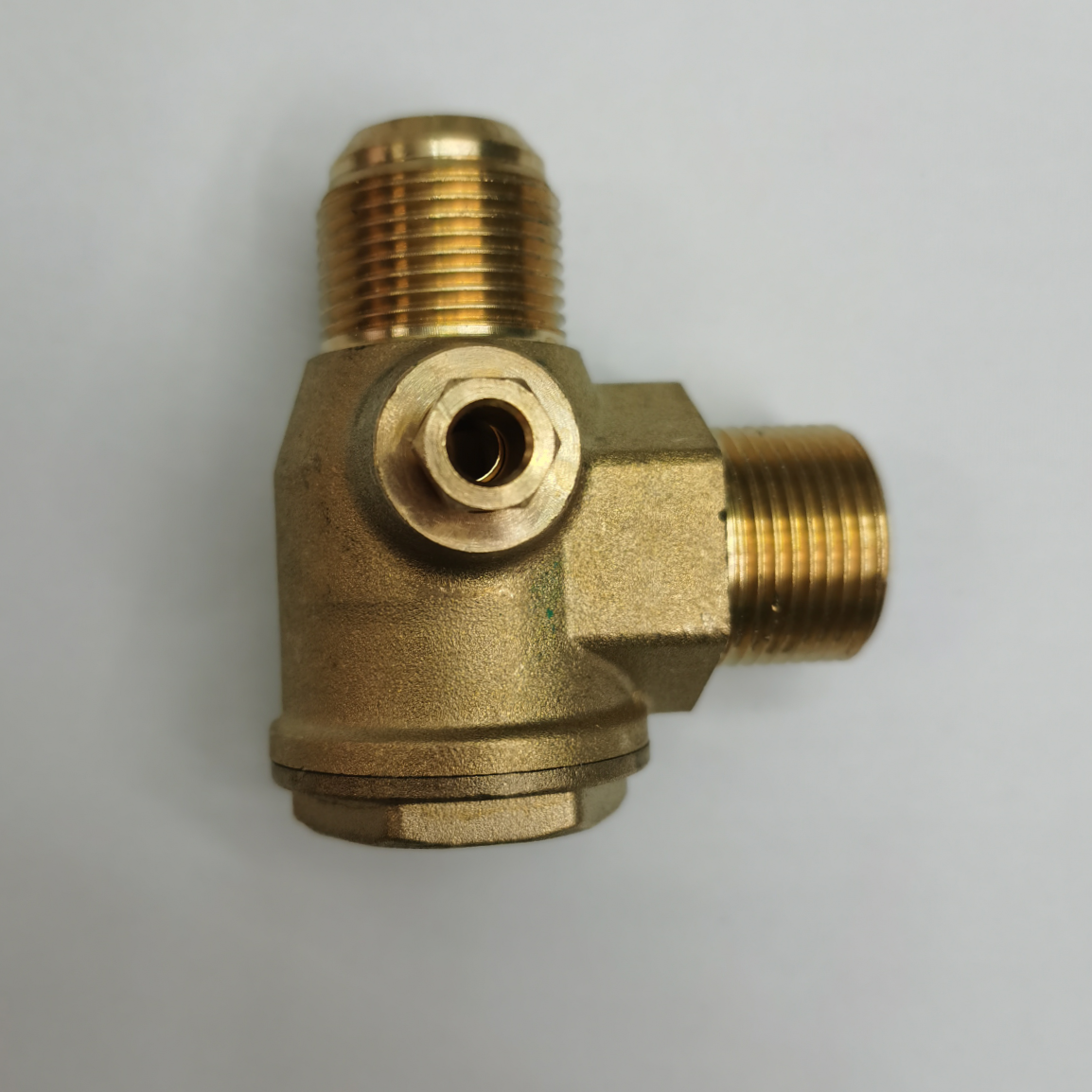
select the appropriate specifications of the check valve, please be sure to consider the following aspects: first, the size of the diameter must match the pipe diameter; secondly, the nature of the working medium determines whether the surface needs special treatment; finally, pay attention to the stability of the temperature range, so as to avoid deformation damage and other issues.
Correct installation is essential: follow the steps to avoid common mistakes
Correct installation is very necessary for any mechanical device, especially when it comes to precision instruments. Here will introduce a set of standard operating procedures, detailing what needs to be paid attention to at each step from preparation to final fixing of screws. It also points out some small problems that are easy to ignore but may lead to serious consequences.
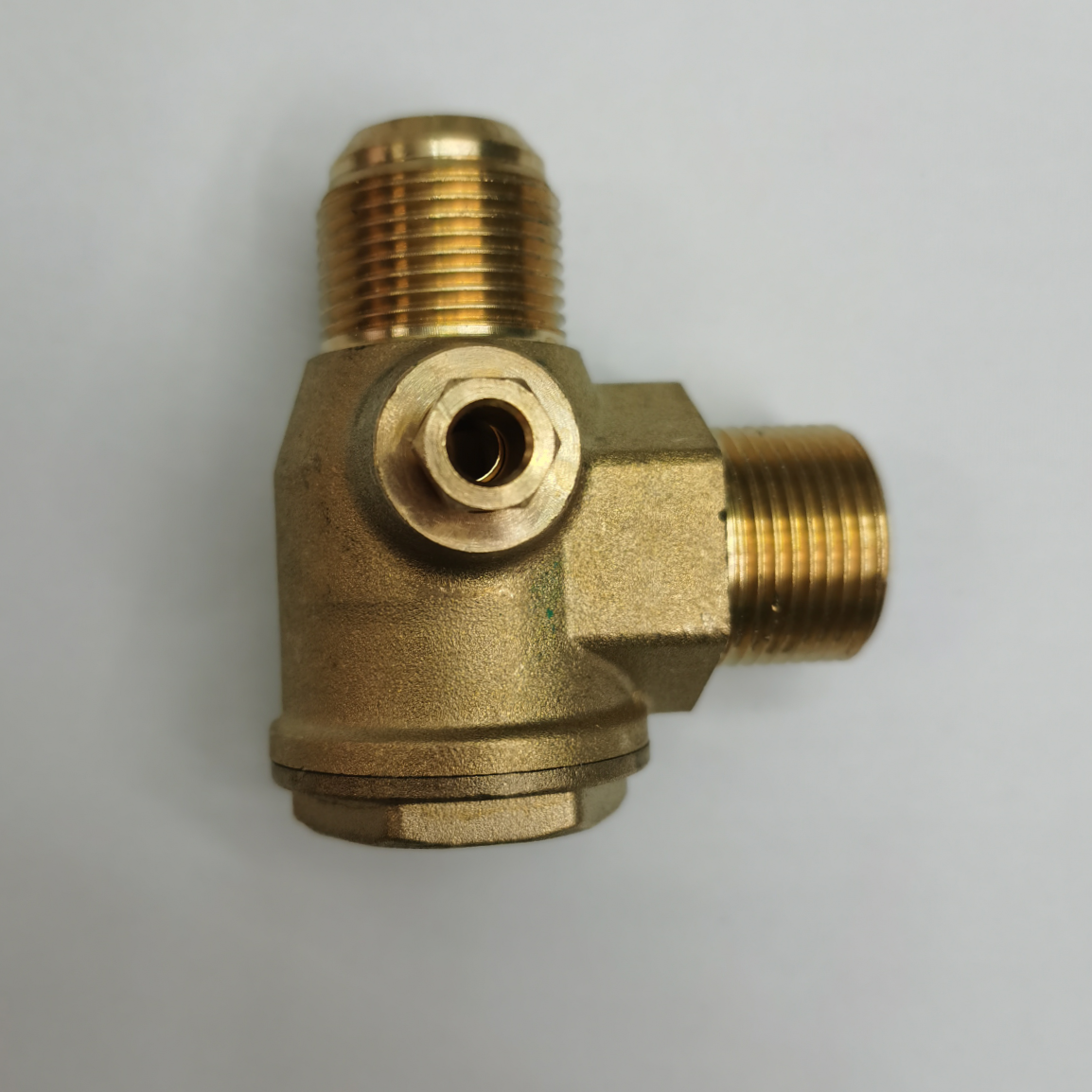
In order to ensure the best working effect, the instructions on the manual should be strictly followed during the installation process. First of all, make sure that all the connection interfaces are clean and apply the right amount of lubricating oil; secondly, before tightening the nut, be sure to check whether the direction is correct; the most important point is to leave enough space for future maintenance and disassembly.
Daily maintenance tips: extend life and keep it in top condition
In order to ensure continuous and stable performance output over a long period of time, regular inspections and appropriate maintenance measures are essential. This article will share a series of practical suggestions, such as cleaning frequency, lubrication site selection and when to replace aging gaskets. It also emphasizes the value of recording historical data, which can help predict future failure risks.
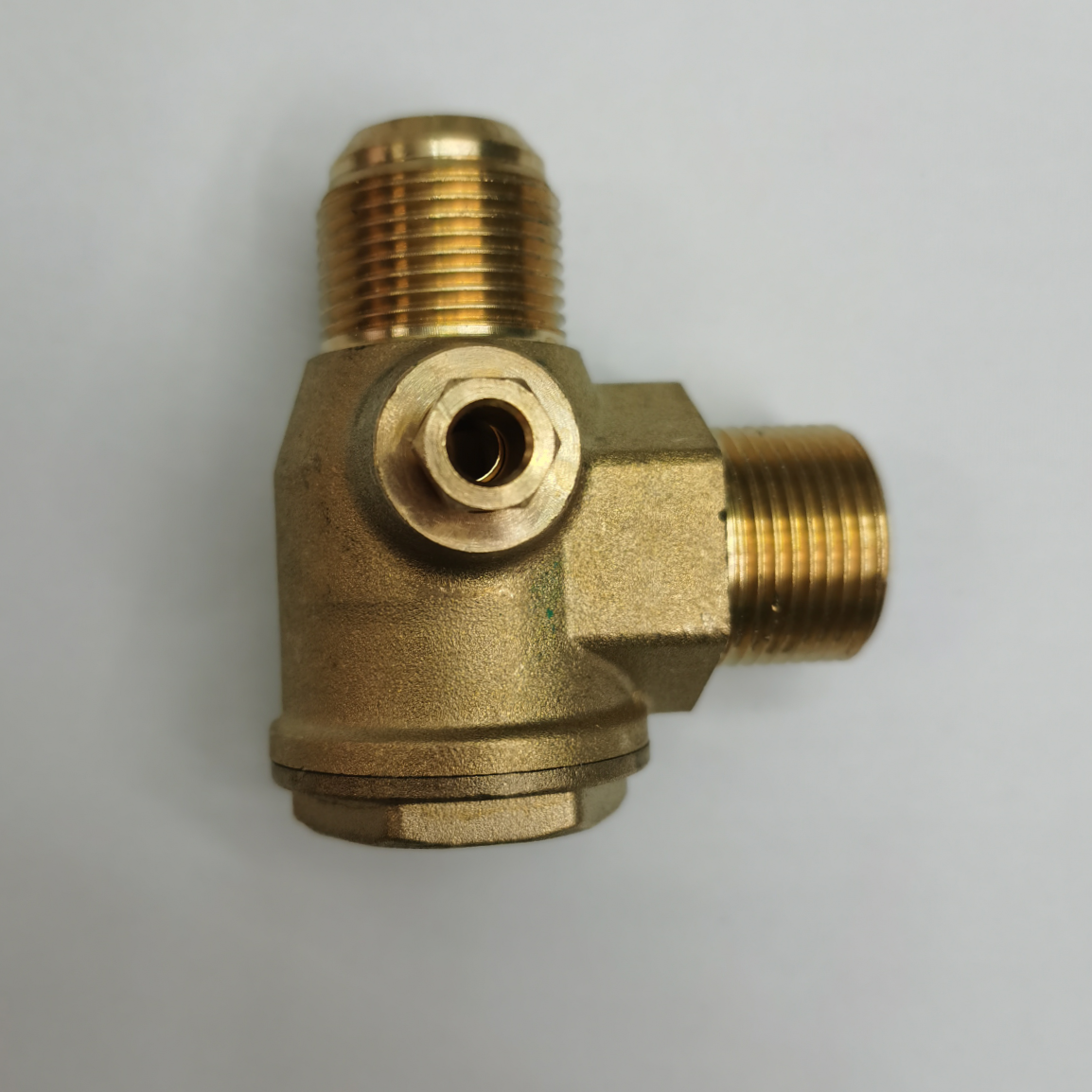
Good maintenance habits can improve the overall life and service quality of the equipment from many angles. Timing removal of dust and debris can effectively slow down the wear rate, and timely supplement of lubricating oil can significantly improve the flexibility of movement. In addition, paying close attention to the changing trend of various operating parameters is also one of the effective means to prevent potential hidden dangers.
Dealing with challenging working conditions: how to adjust the configuration under special circumstances
Sometimes the field environment may not always operate under ideal conditions. What are the special considerations for use in high humidity areas or extreme temperature fluctuations? In this section, we will discuss specific application solutions, such as versions made of corrosion-resistant materials or new generation products with wider temperature adaptability.
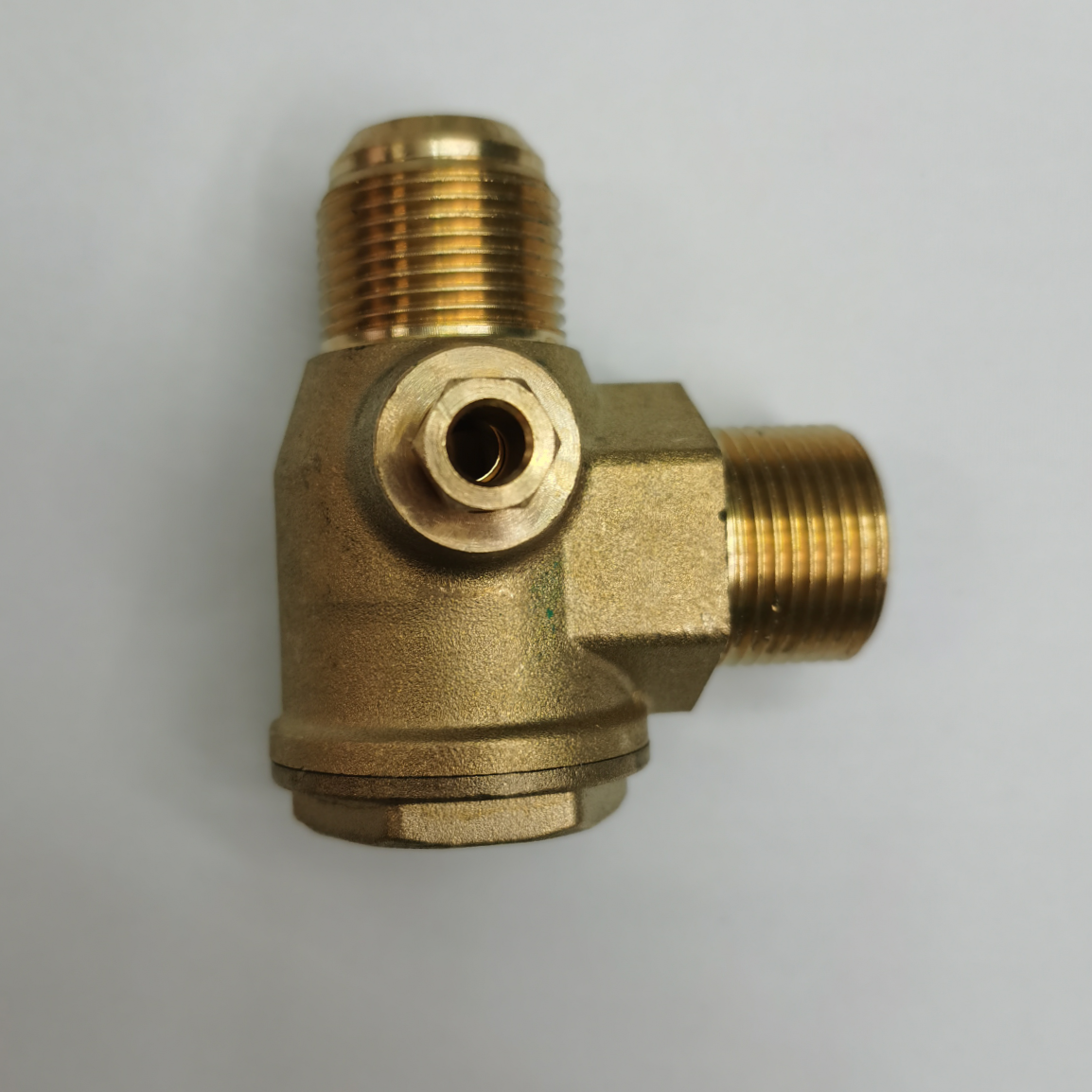
In some special environments, ordinary check valves may face greater challenges. Therefore, the manufacturer has developed a series of improved models specifically designed for harsh conditions. These new models usually use tougher and wear-resistant alloy materials and have undergone rigorous testing