
When we mention air compressors, we usually think of its powerful power and efficient performance. However, behind these bright performances, there is a seemingly insignificant but vital accessory-that is check valve .
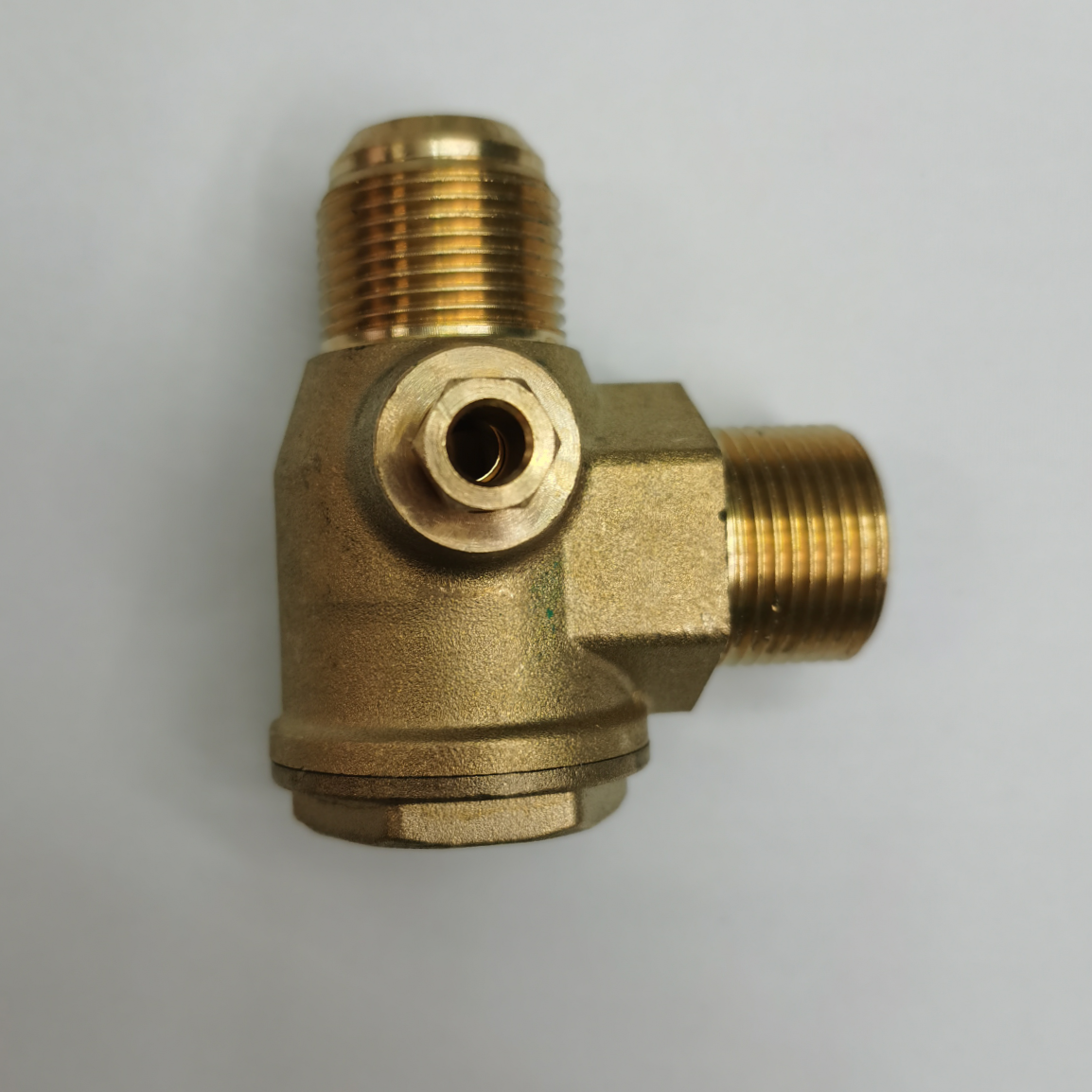
As an important part of the gas flow path, the main function of the 3/4 inch check valve is to prevent reverse flow in the compressed air, thereby protecting the normal operation of the entire system. This small but indispensable design not only ensures effective pressure control, but also significantly reduces the risk of damage due to reverse impact.
So, specifically, how does this check valve achieve its mission? In fact, the principle is very simple: when the compressor produces positive air pressure, the valve opens to allow the gas to pass smoothly; while the negative pressure generated during shutdown or other abnormal conditions causes the valve to close automatically, forming a barrier to prevent any accidental backflow.
There are many types of check valves on the market for consumers to choose from, providing a wealth of options for different usage scenarios and budget requirements. For example, from the material point of view, there are stainless steel, brass and even engineering plastics and other categories to consider; at the same time, we should also pay attention to check the brand credibility of the product and whether the specifications match the requirements of their own equipment.
for the first contact with such devices friends, "how to install?" may be one of the most concerned about the problem! Don't worry, here is a short and easy-to-understand operation guide to help you get started easily:
First confirm the connection position and then tighten the threaded connector in the direction marked until it fits firmly. Then check all joints for signs of air leakage (with soapy water), and finally start the machine to observe the running state to ensure that everything is normal.
Although the operation steps are relatively simple, but in the actual use of the process will inevitably encounter some difficult situations such as sudden failure or excessive noise and other issues how to do? The following are a few common solutions:
-If leakage is found, priority should be given to checking whether the sealing ring is damaged and replacing new parts in time if necessary.
-For abnormal noise, you can try to adjust the installation angle to see if the symptoms can be relieved. Otherwise, it is recommended to contact a professional for on-site maintenance.
-regular cleaning of the accumulation of internal impurities is also one of the effective measures to prevent failure!
in order to better illustrate this problem, let's look at a real case story: a factory workshop neglected the maintenance and update of the original old check valve, resulting in many interruptions in the production line, seriously affecting the production efficiency and increasing the maintenance cost. later, after they decisively adopted the new high-performance products, similar problems never reappeared, fully reflecting the great value brought by high-quality spare parts.
in addition to the correct selection and reasonable maintenance to further improve the overall performance of the compressor unit can also consider other aspects of improvement, such as optimizing the pipeline layout to reduce the resistance of the bend, etc. these are worth trying direction.
of course, the specific styles chosen in different types of application environments will also vary. for example, industrial uses tend to pay more attention to durability and carrying capacity, while home DIY enthusiasts may prefer more cost-effective solutions, which requires us to carefully weigh the pros and cons before purchasing and do our homework.
with the continuous progress of science and technology, I believe that more innovative technologies and design concepts will be applied to the field of check valves in the future, which will surely bring us a better experience. let's look forward to that day!
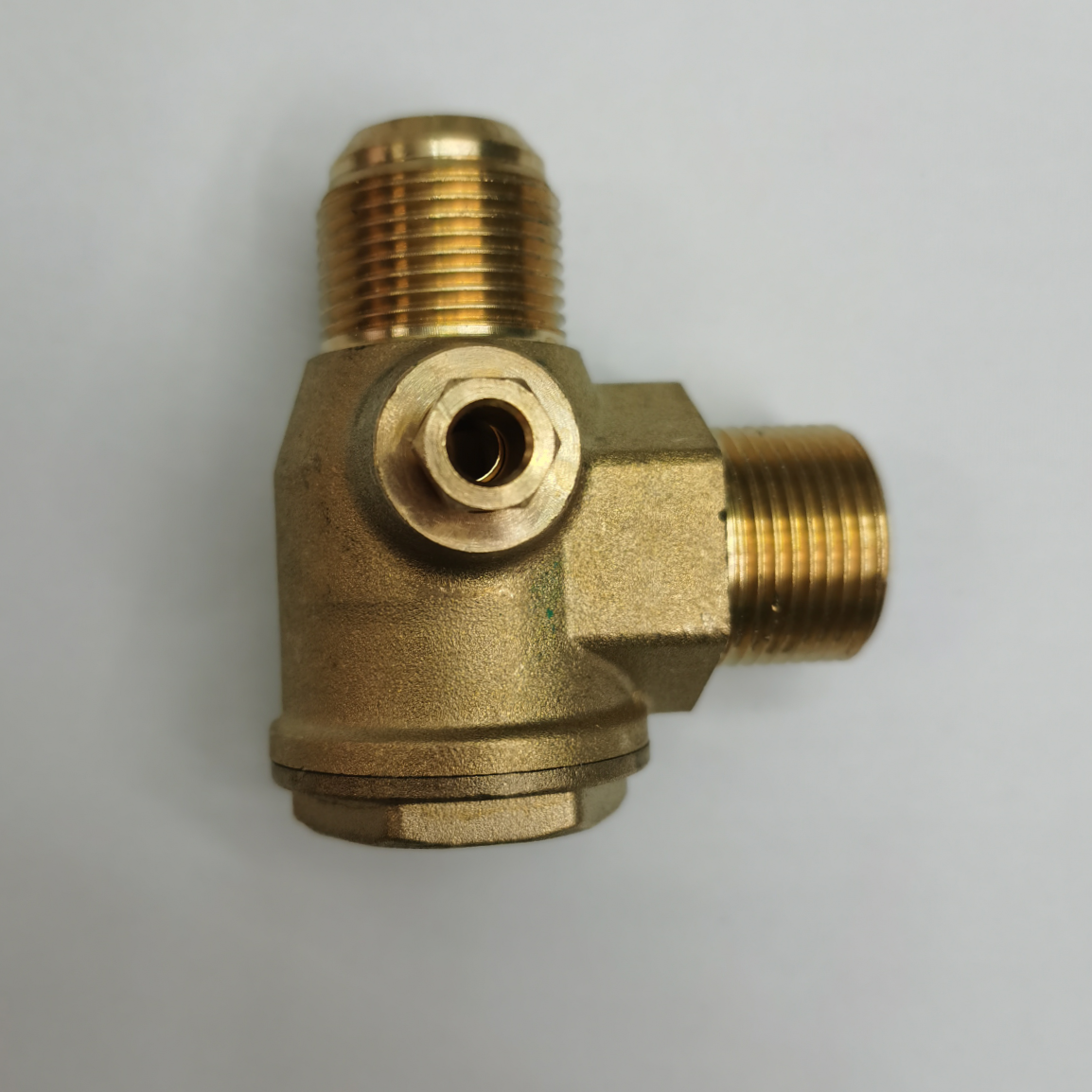