
Reveal the core role of check valve
In the air compressor system, the check valve plays a vital role. Its main task is to prevent any unnecessary reverse flow during the gas flow, thereby protecting the equipment from potential damage. If the check valve fails to work properly or is misconfigured, it may lead to serious consequences, such as unstable air pressure or even pipe burst.
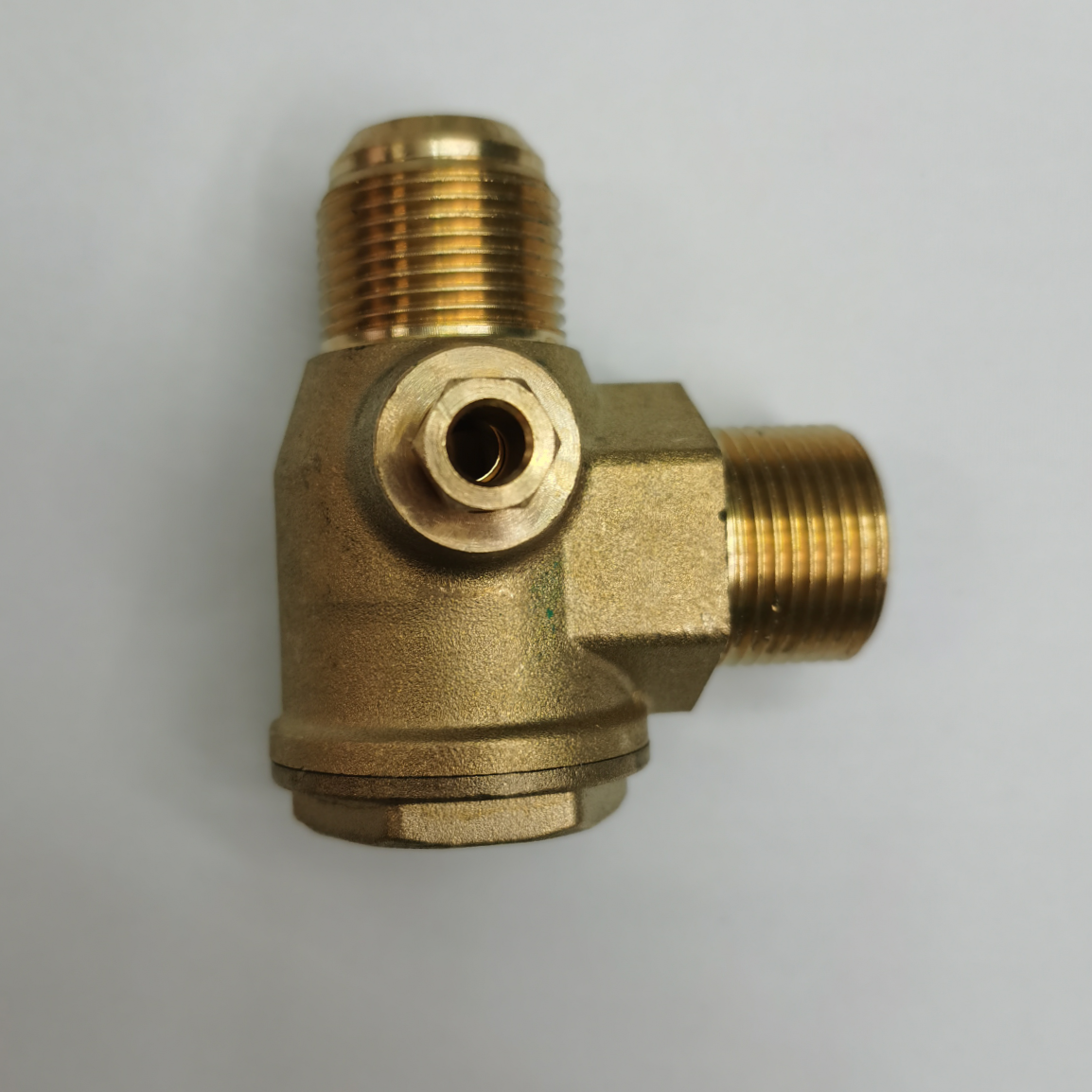
To better understand this, let's look at a specific example: Suppose in a busy factory, an air compressor fails frequently because it does not have the correct check valve. This not only increases maintenance costs, but also reduces productivity due to downtime. Therefore, the selection of appropriate and good quality check valve is essential to maintain the stable operation of the system.
Working principle full analysis
Now let's take a closer look at the specific working mechanism of the 3/4-inch check valve. This valve is composed of several delicate parts, including the spring, the sealing ring and the body itself. When compressed air enters, it pushes the piston to open the channel; once the supply is stopped, the opening position is quickly closed by the force of the built-in spring to prevent the medium from flowing back.
In addition to the basic functions, different types of check valves have their own unique design features. For example, the lift check valve uses a lever mechanism to control the opening and closing action, which has high sensitivity; the swing check valve achieves the same purpose through rotary motion, and is more suitable for application scenarios on large-diameter pipelines.
Material determines quality
High-quality materials are the basis for long-lasting check valves. Typically, manufacturers will choose stainless steel, cast iron, or other special alloys as the main material of construction. Among them, stainless steel has excellent corrosion resistance, especially suitable for long-term use in humid environments; while cast iron is relatively heavy, but it performs well under high temperature and high pressure conditions, and the price is more economical.
However, there are some inferior products in the market. These unqualified check valves are often easy to wear, water leakage and other circumstances, seriously affecting the overall performance. In order to avoid this situation, please be sure to purchase products of well-known brands from regular channels and carefully check whether there are obvious defects or defects on the surface.
Precision Selection Guide
Choosing the right check valve for your needs is not a simple matter. First of all, you need to clarify the requirements of the application, such as the maximum allowable flow rate, operating temperature range and connection size and other information. Next, according to the above parameters, qualified brands and models can be selected for comparative evaluation.
Here is a brief comparative table of the three major brands:
| brand | flow requirements (m/min) | maximum pressure (bar) | |-|-|-| | a | ≥ 1 | ≤ 10 | | B | ≥ 0.8 | ≤ 12 | | c | ≥ 1.2 | ≤ 8 | in addition, attention should be paid to whether the certification and technical indexes of the products are consistent to ensure the purchase of safe and reliable equipment that meets international standards.
Best practices for installation and maintenance
Good installation and regular maintenance can significantly improve the efficiency of the check valve and extend its life. Before installation, please confirm that all parts are in good condition, and then test run for a period of time after assembly is completed step by step according to the instructions in the instructions to check whether there is any abnormal phenomenon. Daily care mainly includes cleaning internal and external dirt, lubricating moving parts and timely replacement of aging components.
we can take corresponding solutions to possible problems. For example, if a slight leakage is found, it can be repaired by tightening the flange screws. If it is seriously damaged, you should contact professionals for on-site maintenance services in time. In short, only by preventing problems before they occur can we get the greatest return on our investment.
Application Scenario Analysis
Finally, let's look at a few successful practical cases. In a large automobile factory, the technician chose a 3/4-inch check valve specially used in the spray shop. The device can not only effectively resist the erosion of spray paint atomization particles, but also durable and not easy to rust, providing a stable air source support for the production line.
Another notable example occurred at a construction site. Due to poor construction conditions, traditional metal valves are prone to sticking problems. After switching to a check valve made of a new composite material, it not only solved this problem, but also reduced the noise level, which won high praise from customers.
Through the summary of these projects, we can learn a lot of valuable lessons. No matter which industry you are in, the reasonable selection of high-quality supporting parts is always the key. I hope the content of this article can help readers achieve better results in future work!
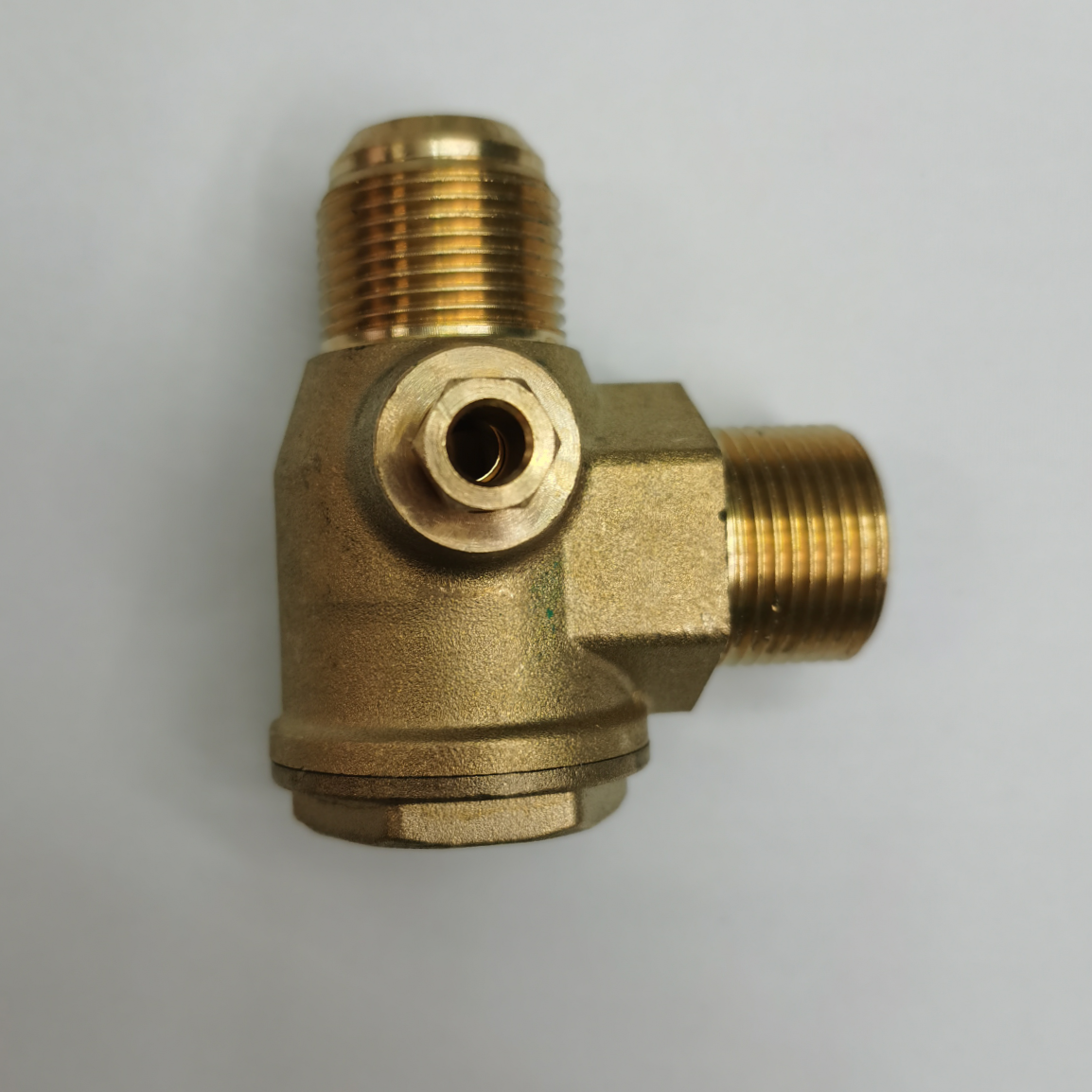