
Discovering the role of the check valve: why it is the heart of the air compression system?
In air compression systems, check valves play a vital role. Its main responsibility is to accurately control the direction of the gas flow, ensuring that the gas can only flow in one direction, thereby avoiding damage or loss of efficiency due to the reverse flow of the gas. Without a check valve, the compressor is exposed to a greater risk of wear and even failure. Therefore, the existence of the check valve greatly improves the stability and safety of the system.
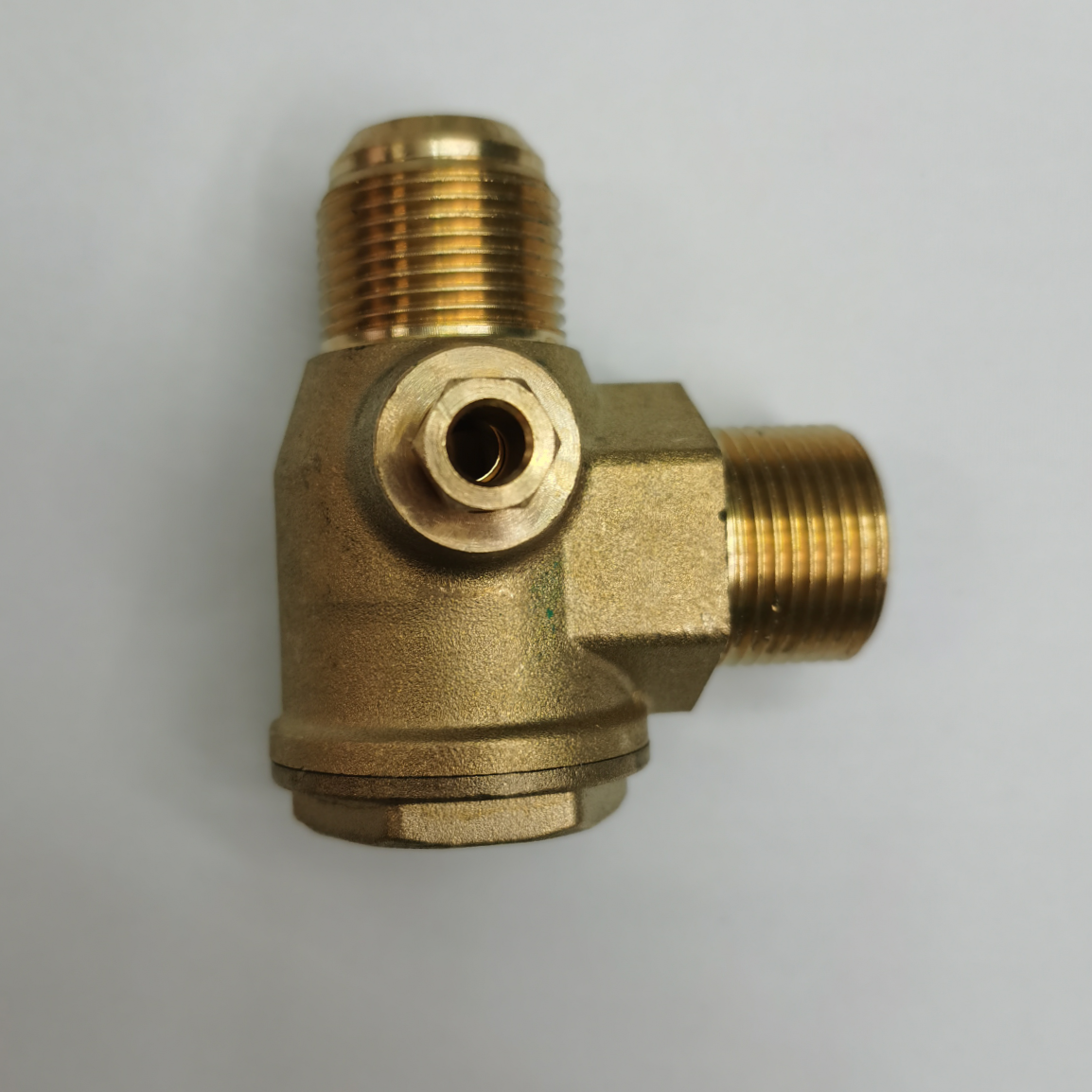
Material determines life: Which material is best for 3/4 inch check valves?
Check valves on the market are usually made of stainless steel, cast iron or engineering plastics. Each material has its unique advantages and application environment. For example, stainless steel has excellent corrosion resistance, which is very suitable for wet or multi-chemical workplaces; cast iron is known for its durability, especially under high load conditions; as for engineering plastics, although the strength is low, but the weight is light and affordable, suitable for low pressure application scenarios.
The key to choosing the right material is to comprehensively consider the requirements of the working conditions, such as the temperature change range, the type of medium, and the need for frequent disassembly. This is the only way to ensure the best performance of the check valve during its life cycle.
Size is not the only standard: how to choose the right size to match your compressor?
Although diameter is an important factor, there are many more parameters to consider when selecting a check valve for a particular air compressor. First of all, it must be clear that the maximum working pressure range and the expected flow value, these data will directly affect the design and technical indicators of the valve.
Suppose a factory uses a check valve that does not meet the rated pressure conditions, which may cause equipment overload operation or leakage at the interface. In order to avoid the occurrence of similar errors, it is recommended to use professional formulas to calculate the ideal configuration before making procurement decisions.
Installation Tips Sharing: Ways to Make Your Check Valve Get Twice the Results with Half the Work
In order to make the check valve better serve the air compression system, please follow the following standardized operation process for assembly:
The first step is to confirm that all parts are intact and assemble the parts according to the drawing instructions.
The second step is to use appropriate tools to complete the pipeline docking operation, and apply an appropriate amount of lubricating oil to improve the friction coefficient.
the third step must do a good job of sealing ring pre-tightening treatment to prevent leakage accidents.
In addition, there are several thoughtful tips for reference, such as reserving enough maintenance space in advance to facilitate future maintenance and updates, and regularly applying rust inhibitor to extend the service life of hardware.
The secret weapon of return on investment: correctly maintaining the value of extended service life
Good maintenance habits can not only significantly reduce the cost of subsequent repairs, but also continuously improve the overall level of operation. For example, set up a fixed periodic inspection mechanism to clean up the internal impurity accumulation area in time; In addition, when any abnormal situation is found, the cause should be investigated in time to take corrective measures so as not to cause more disaster.
each user should be tailored to their own actual situation of the exclusive maintenance plan, so as to truly tap the potential economic benefits of the component potential.
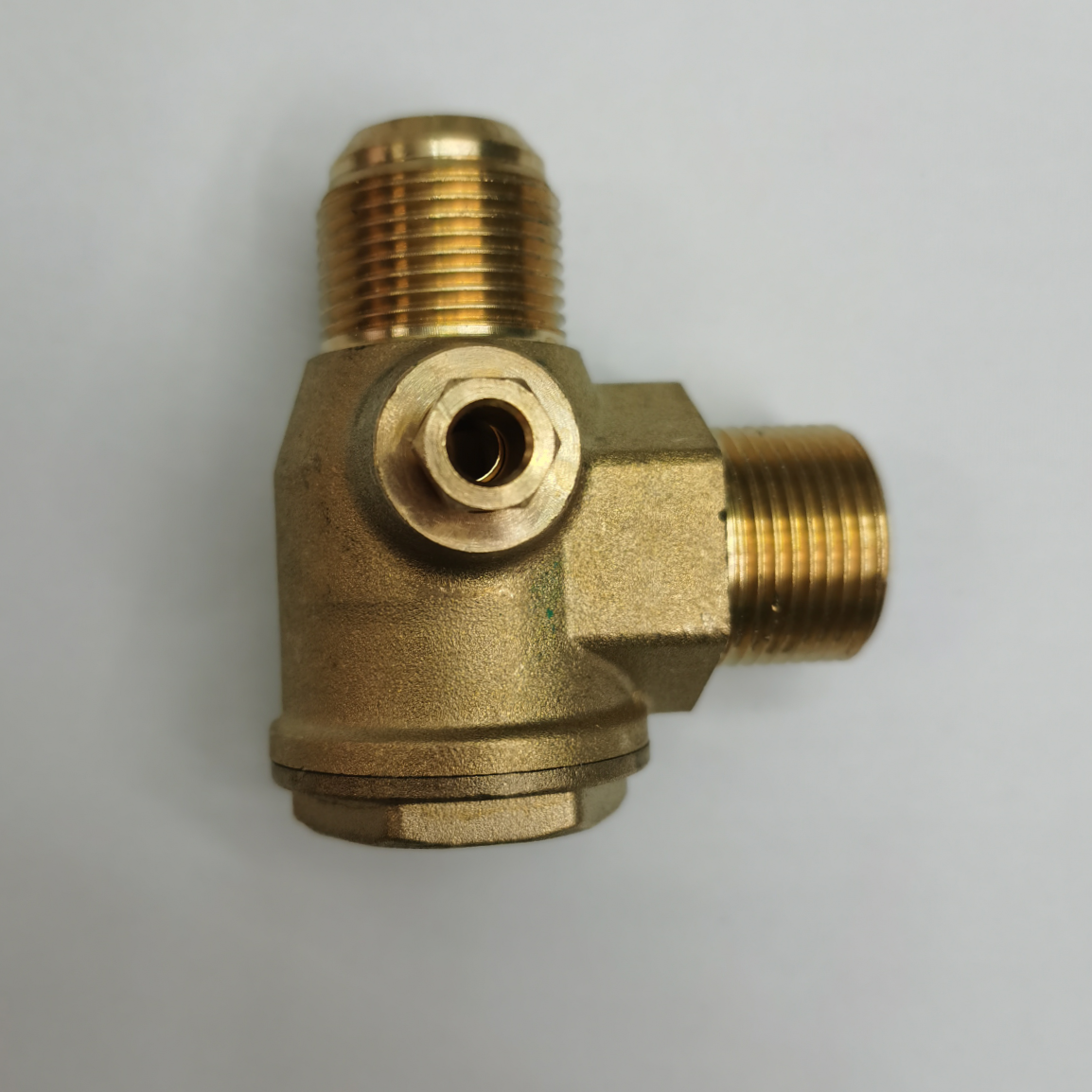