
The importance of check valves: the key to ensuring the stable operation of the system
In industrial production and daily life, air compressors are widely used. One of the key components-check valve, although the volume is not large, but the role can not be ignored. The main function of the check valve is to prevent backflow when the system pressure is abnormal, thereby protecting the safe operation of the equipment. Especially in a high-pressure environment, a check valve with excellent performance can greatly reduce the probability of failure and extend the service life of the equipment.
Understanding 3/4-inch Check Valves: Basic Parameters and Applicable Scenarios
The 3/4 inch check valve is a commonly used air compressor accessory. Its main parameters include caliber (3/4 inch), maximum working pressure, and working temperature range. Check valves of this size are suitable for various small and medium-sized air compressor systems, especially in homes and small factories. Due to its compact design and high cost performance, the 3/4 inch check valve has become the first choice for many users.
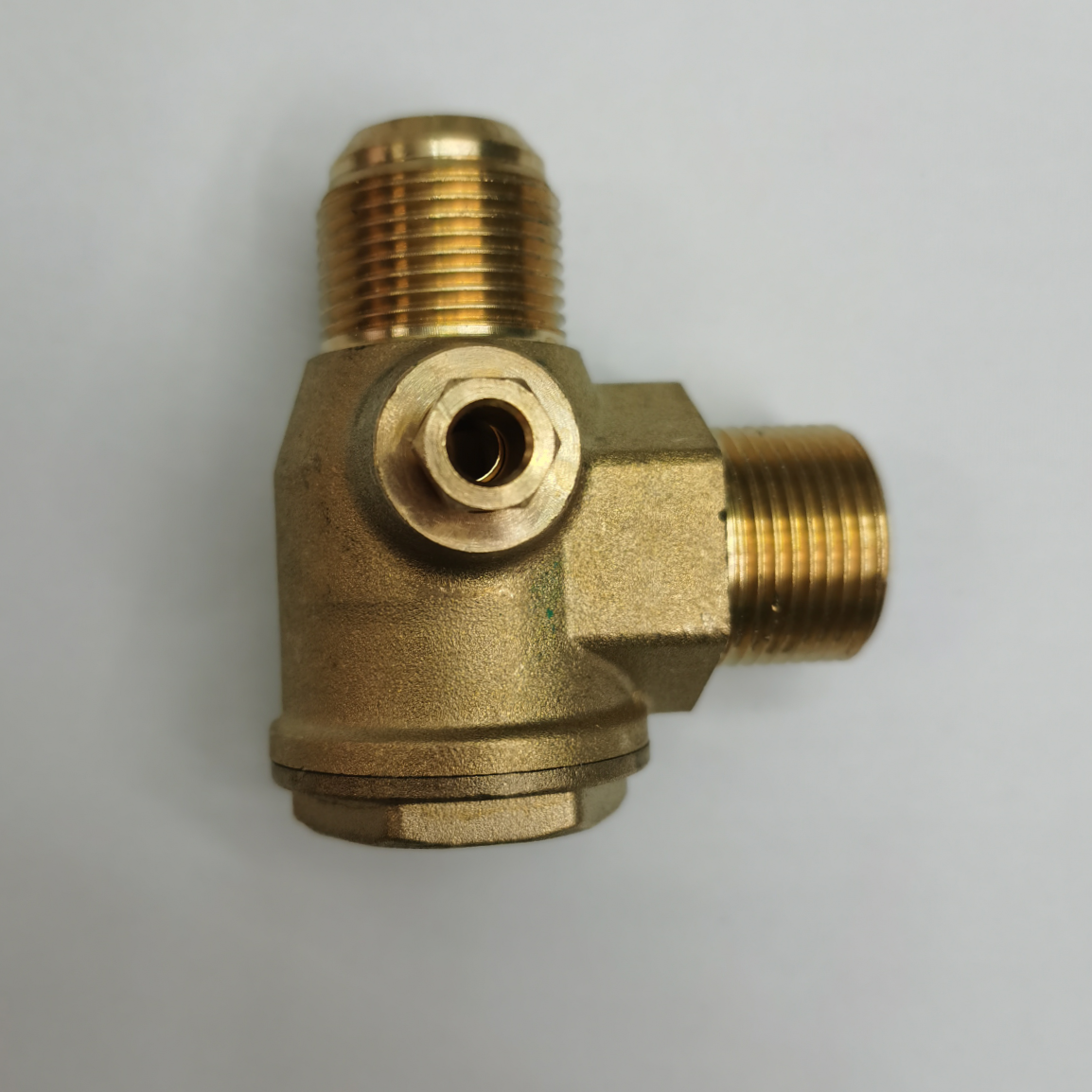
In-depth analysis: the working principle of the 3/4 inch check valve
The 3/4 inch check valve controls the direction of gas flow through the internal spring and disc. When the pressure in the system exceeds the set value, the valve flap will be pushed open to allow the gas to flow normally; once the pressure drops below the set value, the valve flap will automatically close under the action of the spring force to prevent the gas from flowing back. This simple and effective mechanism ensures the safe and stable operation of the system.
Quality Difference: How to Distinguish High Quality Check Valves
There are many brands of check valves on the market, and the quality is uneven. Choosing a high-quality check valve can start from the following aspects: First, check the product's certification marks, such as ISO, CE, etc., these marks indicate that the product has undergone strict testing and certification; secondly, pay attention to the choice of materials, high-quality The check valve is usually made of corrosion-resistant, high-strength metal materials; finally, the product quality can be judged by user evaluation and reputation.
Installation guide: How to install the check valve correctly
The correct installation method is essential for the best performance of the check valve. Before installation, please ensure that the inside of the pipeline is clean and free of impurities, so as not to affect the sealing of the valve. When installing, pay attention to the direction of the check valve and ensure that the arrow points to the direction of gas flow. After the installation, a leak test is required to confirm that there is no air leakage.
Troubleshooting: Common Problems and Solutions in Daily Use
Although the structure of the check valve is simple, some problems may still occur during long-term use, such as leakage, jamming, etc. When encountering these problems, first check whether the check valve is installed correctly, followed by cleaning the impurities inside the valve body, and replacing new seals if necessary. If the problem still cannot be solved, it is recommended to contact professional and technical personnel for maintenance.
Maintenance: Tips to extend the life of check valves
Regular maintenance can significantly extend the service life of the check valve. It is recommended to conduct a comprehensive inspection of the check valve at regular intervals, including removing dirt on the inner wall of the valve body and checking the status of the seal. In addition, when not in use, it is best to store the check valve in a dry and ventilated place to avoid moisture and corrosion.
Case Study: Successful Application Example Sharing
A small and micro enterprise in Jiangsu has significantly improved its production efficiency after introducing an air compressor system equipped with a 3/4-inch check valve. Prior to this, due to the lack of effective non-return device, frequent air pressure fluctuations caused the equipment to be frequently shut down for maintenance, which seriously affected the continuity of the production line. Since the installation of this check valve, the company has not only solved this problem, but also reduced energy consumption costs, and achieved a win-win situation for economic and social benefits.
Purchase Points: Several Considerations for Selecting the Right Check Valve
When purchasing check valves, in addition to the basic technical parameters, the following factors need to be considered comprehensively: first, application scenarios, different working conditions may require different check valve types; Second, budget, high-performance products are often more expensive, but more economical in the long run; Third, after-sales service, good after-sales support can get help in time when problems arise.
Market Trends: Future Development Direction of Check Valves
With the progress of science and technology, the future of the check valve will be more intelligent and environmentally friendly. On the one hand, intelligent monitoring technology and remote control system are expected to be integrated into the check valve to realize real-time monitoring and fault warning of equipment status; on the other hand, check valves made of renewable materials will become a new trend in the development of the industry, helping to build a green and low-carbon society.
Environmental Considerations: Green Manufacturing Practices
As a responsible manufacturer, we are committed to promoting environmental protection. In the process of producing 3/4-inch check valves, we strictly follow international environmental protection standards, use low-pollution, easy-to-recycle materials, and constantly optimize the production process to minimize the impact on the environment. We believe that only by adhering to the road of sustainable development can we win the recognition of the market and the trust of consumers.