
why 3/4 inch check valve is indispensable: the secret weapon to ensure the operation of the compressor
In the air compressor system, there is a small component that plays a vital role-that is, the 3/4-inch check valve. Although it may seem trivial, it is this humble element that effectively prevents the reverse flow of gas and protects the entire machine from potential damage. Imagine the risks of a compressor operating in a high-pressure environment without such a "guardian"? The answer is obvious.
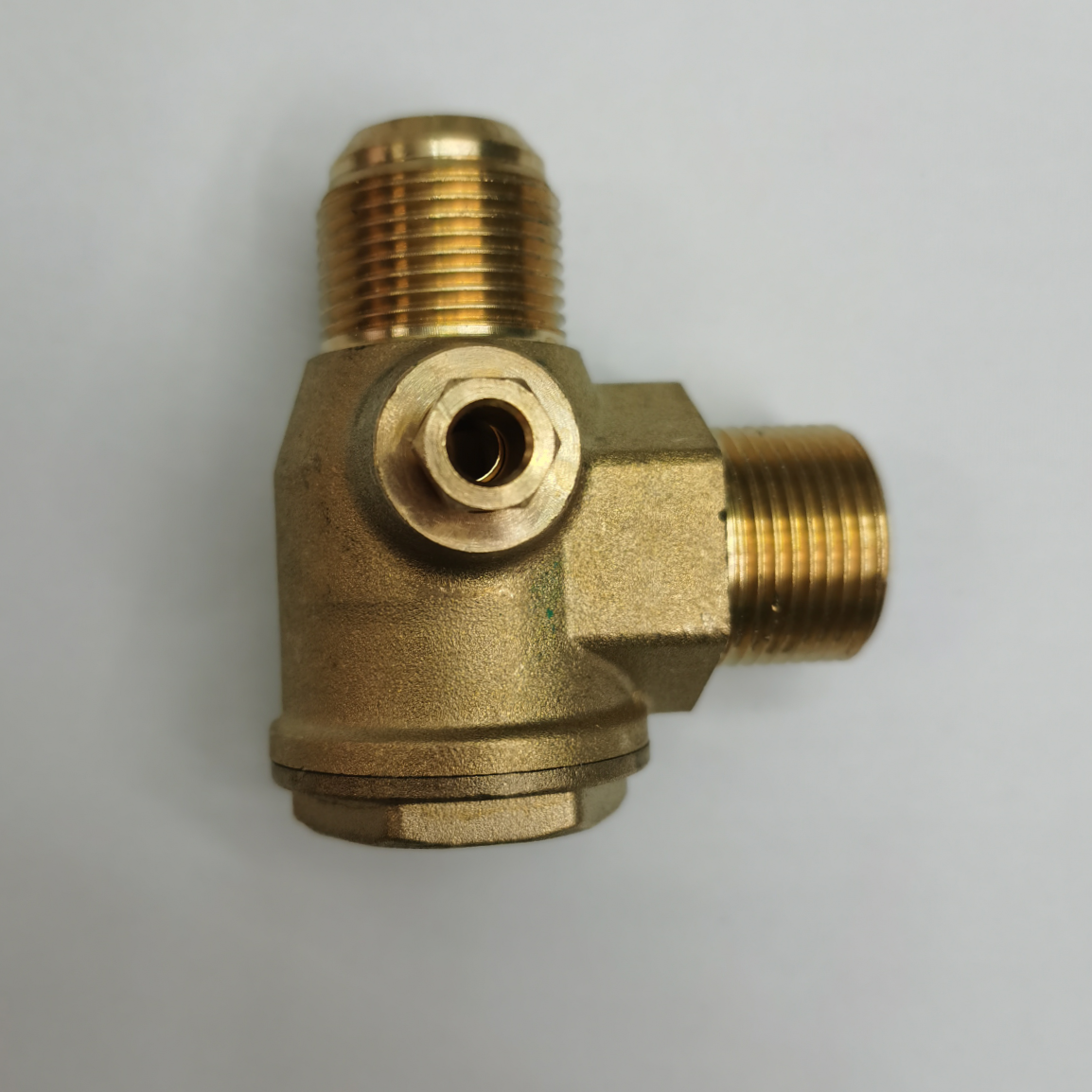
There have been such examples in practical applications: a small processing plant failed to pay attention to this detail, resulting in frequent failures, which seriously affected the production schedule. After professional testing found that the original is the use of the check valve size is not appropriate. Therefore, in the purchase must be cautious about this link, because the wrong configuration will not only affect the work efficiency may also cause security risks.
Materials and Construction: Durable and Efficient Protective Barriers
The reason why high quality check valves can play an important role for a long time depends largely on their carefully selected production materials and exquisite production technology. At present, most of the mainstream products on the market use a combination of metal alloys and synthetic rubber, the former provides excellent strength support, the latter enhances the sealing performance. This combination makes the valve both robust and flexible in response to changes in internal and external conditions.

Not only that, the application of precision machining technology has also greatly improved the service life of the product. Fine grinding and assembly through automated production equipment, each interface has reached a near-perfect fit, reducing the possibility of air leakage due to loosening. In this way, not only can shorten the maintenance cycle, but also effectively control operating costs.
Diversified application scenarios: from the factory floor to the home garage
Whether you are running around the clock on a large manufacturing assembly line or performing an occasional simple DIY task in a home garage, you will find that almost all air compression equipment will be equipped with at least one check valve. This is because they are widely used in various fields, adaptable and versatile.

According to the specific needs of different environments, manufacturers have developed distinctive styles for consumers to choose from. For example, when working under high temperature conditions, you can choose the heat-resistant type; if you are worried about corrosion, there are products with special anti-corrosion coatings to consider; and for those who want to complete the disassembly and assembly easily and quickly, the quick plug connector is undoubtedly The best helper.
Precise Selection Guide: Finding the Perfect Solution
In the face of a wide range of market options, how to accurately determine which one is the most suitable for you? This requires a series of key technical indicators for comparative analysis. We usually focus on the following areas:
- Flow range: Determine the minimum and maximum values according to the amount of conveying medium required;- Maximum working pressure: The expected load must be exceeded to ensure the safety factor;- Connection method: Whether the thread, flange or other form is convenient for the existing pipeline to connect.

In addition to the above hard criteria, there are some lessons learned that can help beginners get started faster. For example, try to give priority to products produced by well-known brands; carefully read the parameters in the instructions and check with the actual situation. As long as the master of these basic knowledge to believe that anyone can find a satisfactory answer.
Installation and debugging skills: let the novice can easily handle
It may be a bit tricky for people who come into contact with such mechanical parts for the first time, but in fact, as long as you follow the correct steps step by step, you can complete the whole process independently. First of all, we must prepare the necessary toolbox, such as wrenches, screwdrivers and other regular supplies must be indispensable; the second is to pay attention to personal protective equipment to wear complete to avoid accidental injury.

the following is to refer to the accompanying drawings or watch the teaching video to operate step by step until all are in place. In case of difficulties, there is no need to worry. There are many free resource sharing platforms on the network that can provide valuable reference materials and support services. Finally, don't forget to regularly review the condition of the fasteners to ensure that everything is working properly.
Troubleshooting Handbook: An Effective Way to Solve Everyday Problems
Even the best product quality cannot completely eliminate all possible failures, so learning to identify and eliminate common problems is one of the necessary skills for every user. Here are some of the most common phenomena and their corresponding treatments:
- -If leakage is found, please check the sealing ring for signs of aging and replace it if necessary;
- -If it cannot be opened or closed, it may be blocked by excessive accumulation of internal impurities. At this time, rinse it with clean water and try again.
- -If hearing the abnormal noise does not rule out the cause of bearing wear, it is recommended to stop using it immediately and send it for repair inspection.

In addition to develop good maintenance habits, regular cleaning of filters, lubrication of moving parts and other work can not be ignored. Only in this way can the service life be extended to the greatest extent and always maintain an efficient working state.
Improving Efficiency and Economic Benefits: Return on Investment
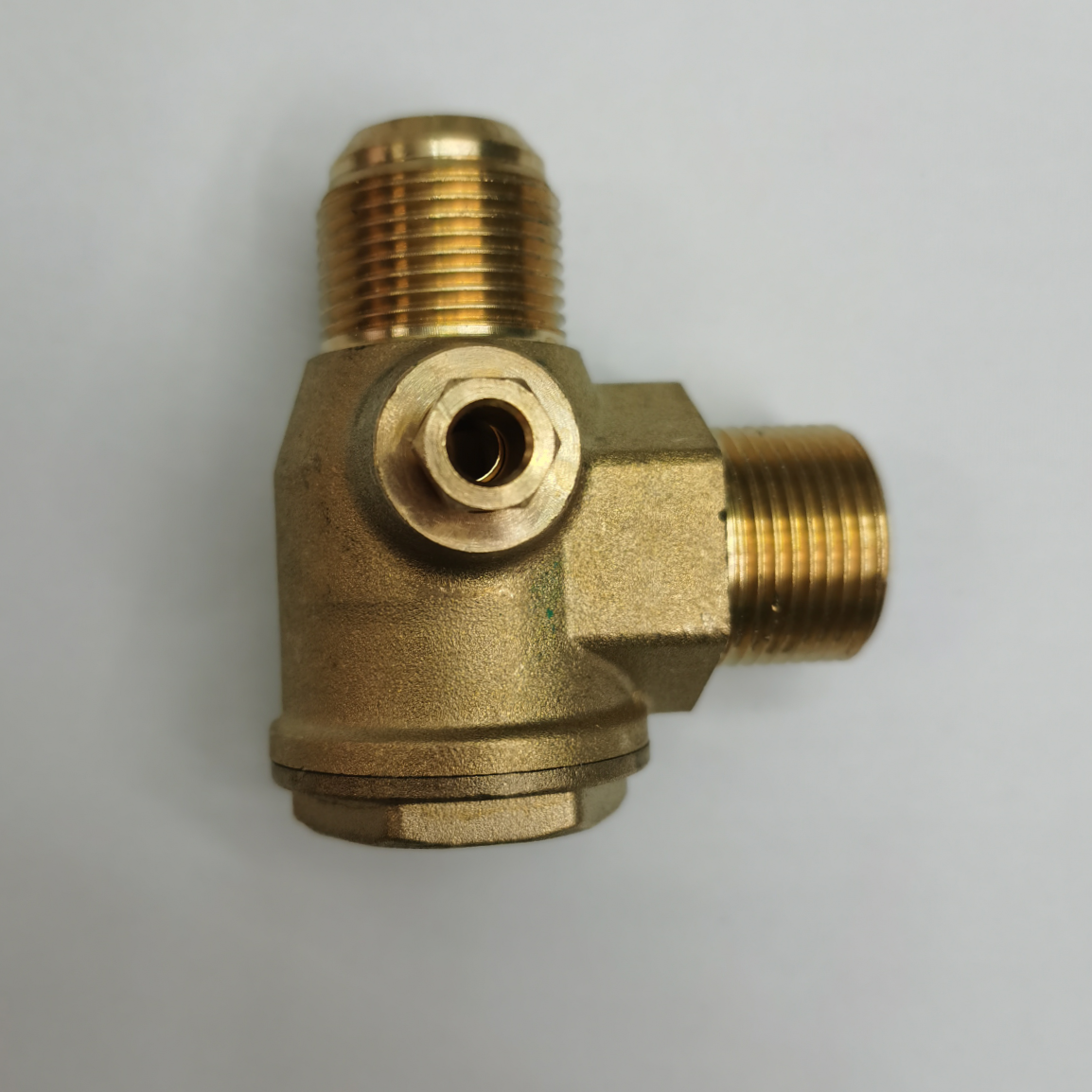