
In the field of industrial production and home maintenance, air compressors have become one of the indispensable tools. However, many people may overlook one of the important but easily overlooked components-the role of the check valve. Today, let's take a closer look at how this efficient 3/4 inch check valve can ensure the stable operation of your air compression system.
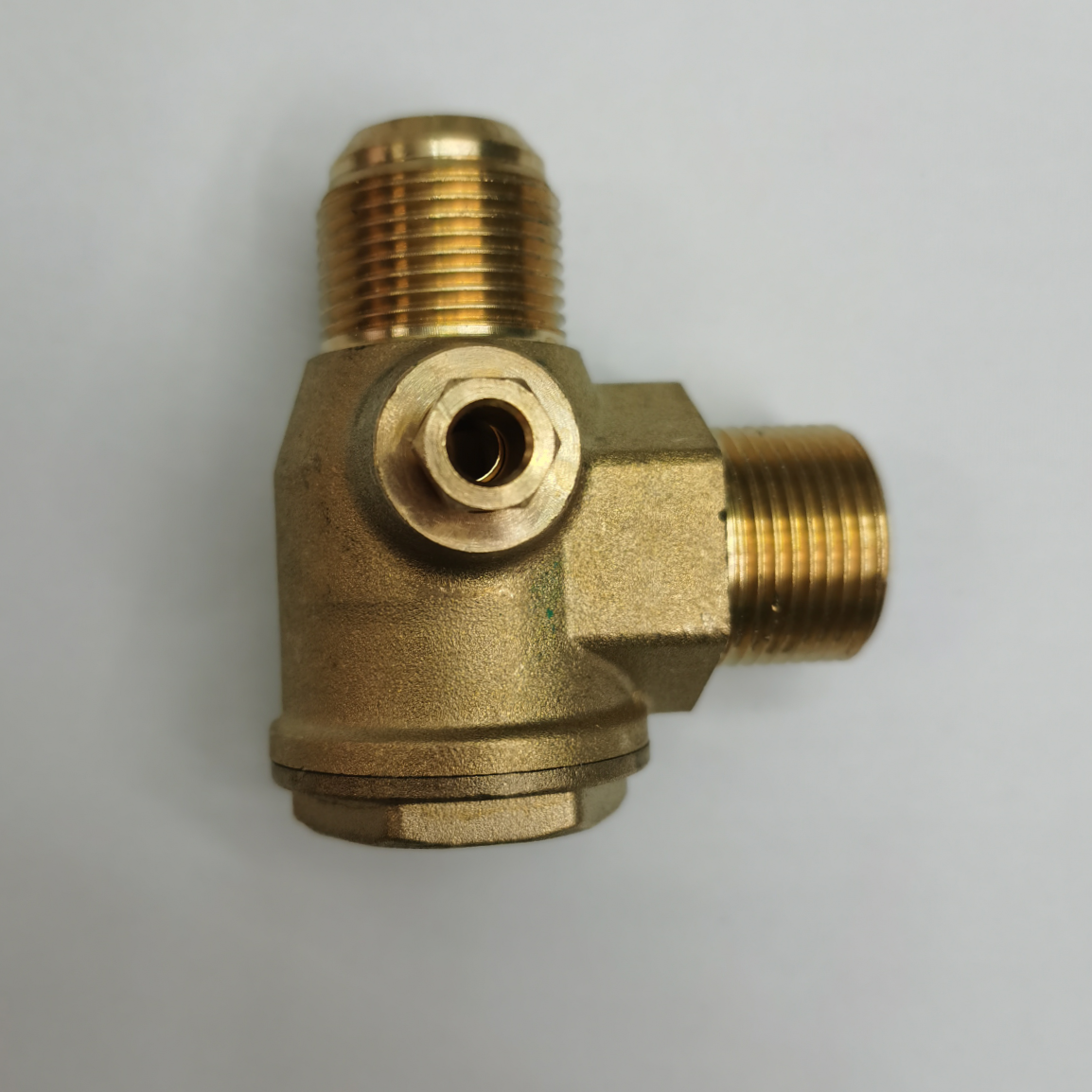
Analysis of core components: the role of check valves in air compression systems cannot be underestimated
The main task of the check valve is to prevent the occurrence of backflow in the compressed air, which is essential to protect the motor and other sensitive components. If there is no proper non-return mechanism, it may cause gas to flow back into the pump when the machine is shut down, which may cause damage or even safety accidents. In addition, good unidirectional flow control can also reduce energy loss and maintain a constant voltage output state.
Material and Process: Key Elements of high quality Check Valves
In order to achieve the above functional advantages, we recommend choose products made of corrosion-resistant stainless steel materials with excellent sealing performance. This type of valve not only has a long service life but also can work in harsh environments without losing efficiency. At the same time, precision machining technology ensures that each part size is accurate to achieve the ideal matching degree to reduce the risk of leakage.
Installation manual: hand to teach you the correct assembly of the check valve
Although it sounds complicated, in fact, the assembly process can be completed smoothly as long as the instructions are followed. First, it is necessary to confirm whether the diameter of the pipe used meets the requirements (standard 3/4 inch in this case), and then connect the inlet and outlet interface parts in turn and fix them by threaded fasteners. Finally, don't forget to conduct a leak test to verify the overall structural integrity.
Performance data interpretation: why the 3/4 inch check valve is so reliable
After a number of rigorous tests, these models can continue to operate in the pressure range of up to 1MPa without significant deformation or failure. In addition, its internal spring device can adjust the opening pressure value, which makes the adaptation range more extensive to meet the flexible application possibilities under various demand conditions.
Scenario adaptation analysis: how to select the appropriate check valve model under different working conditions
Although the current discussion is about the application prospect of a specific size design version, if you face other scale projects, you must consider factors such as flow size, medium properties, and ambient temperature before making a decision. For example, for high humidity sites, it is recommended to give priority to the use of all-copper body structure to prevent corrosion problems; and during high temperature area operation, special attention should be paid to whether the filler selection can withstand the corresponding heat to avoid unexpected consequences.
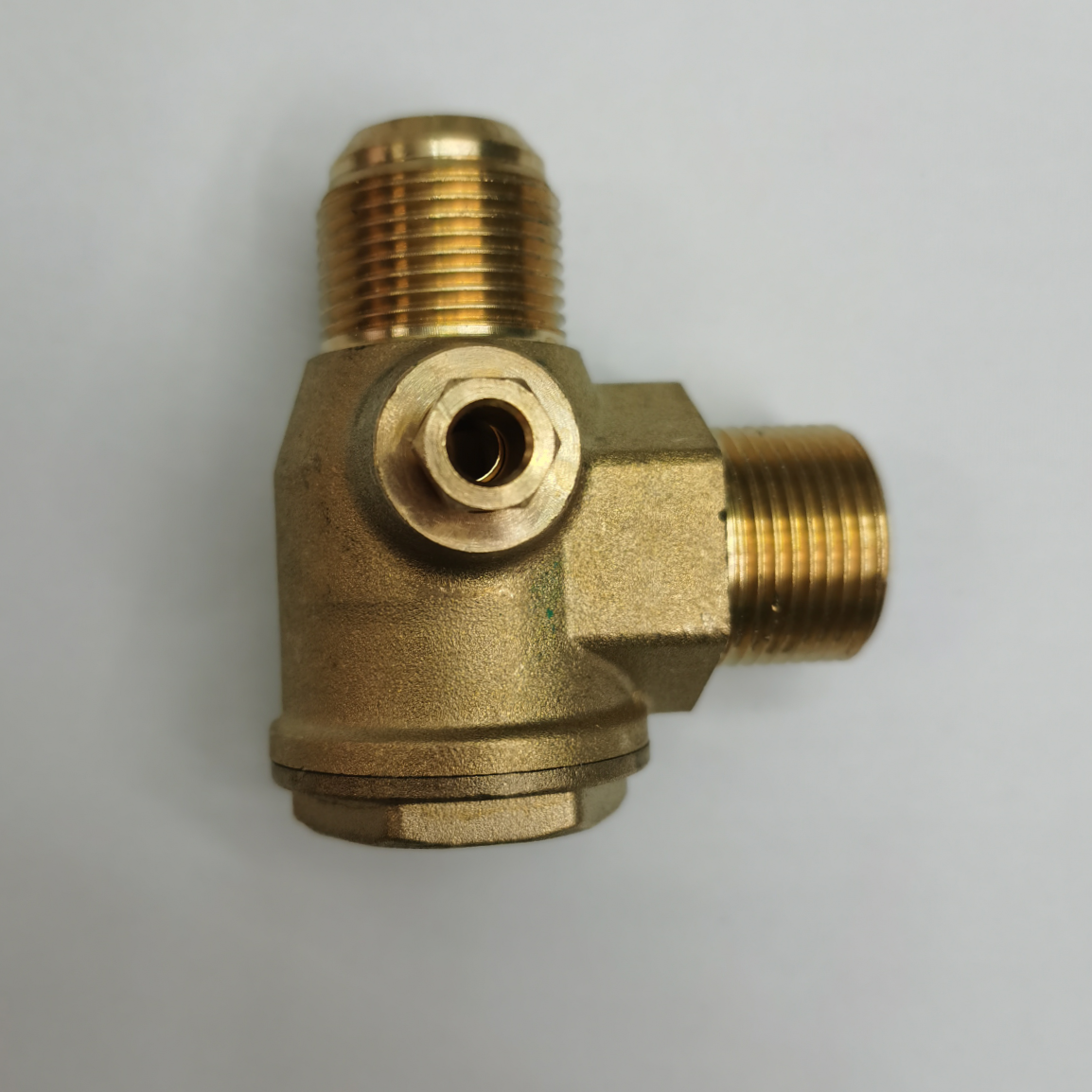