
Air compressors play an important role in industrial production and household maintenance, and the check valve, as one of its key accessories, can effectively prevent gas backflow and protect the safe operation of equipment. This article will detail the functional characteristics, installation methods and maintenance techniques of air compressor check valves to help you choose the most suitable check valve to improve equipment performance and work efficiency.
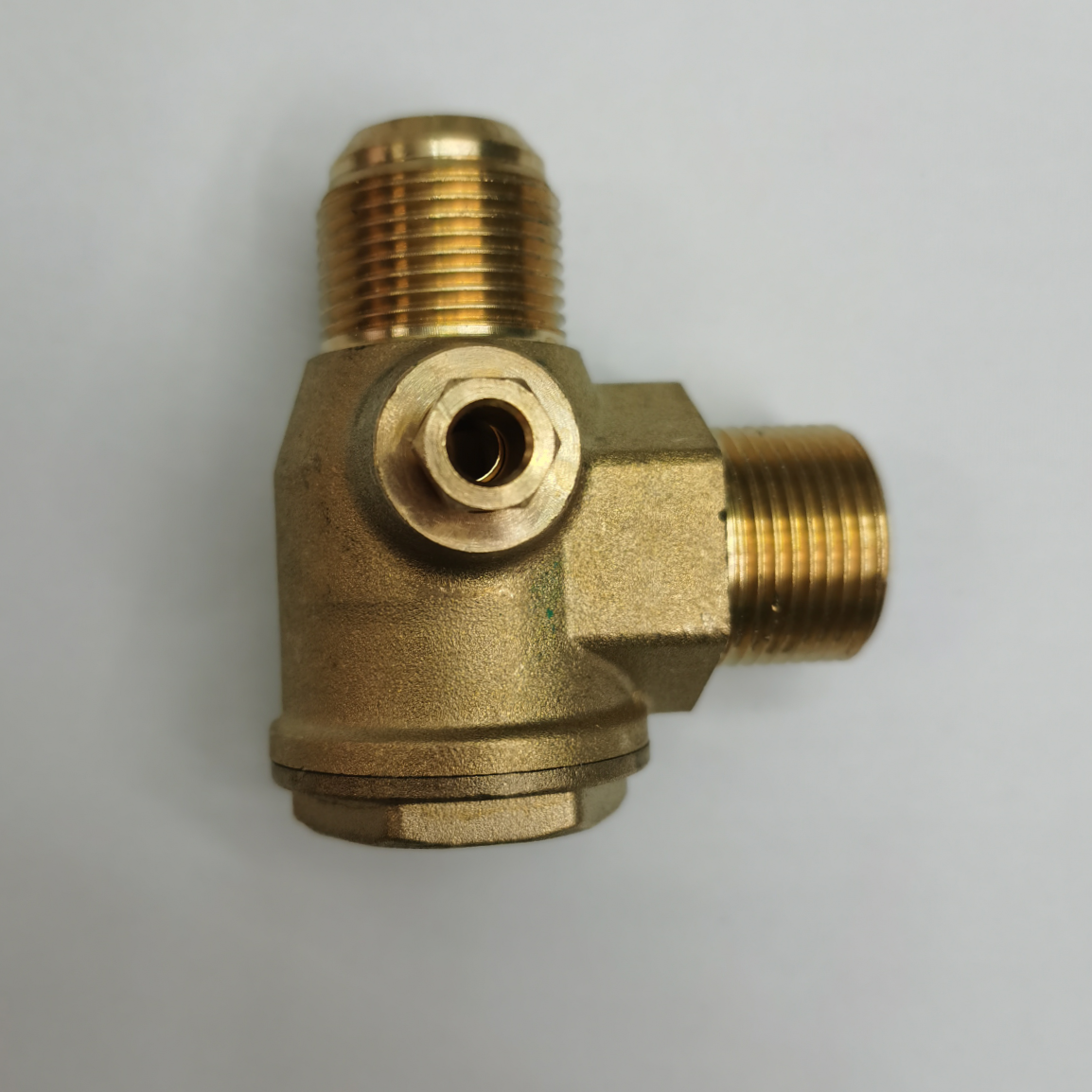
The importance of air compressors
Core Roles in Industrial Production
In modern industrial production, air compressors are the core equipment of many manufacturing processes. From automobile manufacturing to food processing, from chemical production to electronic assembly, the high-pressure gas provided by air compressors is an important power source for driving various mechanical equipment. Its stability and reliability directly affect the efficiency of the production line and product quality.
The right-hand man for home maintenance
In home maintenance, air compressors also play an important role. Whether it is painting, nailing or inflating, the air compressor can provide powerful pneumatic support. Especially in the hands of DIY enthusiasts, an efficient air compressor can greatly improve the convenience and quality of work.
Function and necessity of check valve
Prevention of gas backflow
The main function of the check valve is to prevent the gas from flowing back and ensure that the gas can only flow in the predetermined direction. This is essential to maintain the normal operation of the system, especially in the multi-stage compression system, the check valve can prevent the high-pressure gas from flowing back into the low-pressure pipeline to avoid equipment damage.
Protect safe operation of equipment
By preventing reverse flow of gas, the check valve also protects the air compressor and other related equipment from damage. For example, in the event of a sudden power failure or other emergency situations, the check valve can be quickly closed to prevent equipment failure and safety accidents caused by high-pressure gas impact.
The working principle of the check valve
One-way flow mechanism
There is a movable flap or piston inside the check valve. When the gas flows forward, the flap is pushed open to allow the gas to pass; when the gas tries to flow back, the flap will automatically close to prevent the gas from flowing back. This simple mechanical design ensures a unidirectional air flow.
Pressure Sensitive Design
The check valve usually has a pressure-sensitive design, that is, the flap will open only when the pressure of the air inlet exceeds a certain threshold. This helps to save energy, reduce unnecessary airflow losses, and improve the overall efficiency of the system.
Main types of check valves
Spring-loaded check valve
Spring-loaded check valves are one of the most common types. It uses the elastic force of the spring to control the opening and closing of the flap. When the pressure of the air inlet is greater than the preload of the spring, the flap is pushed open and the gas passes through; when the pressure decreases, the spring pushes the flap back to its original position and closes the channel.
Gravity check valve
Gravity check valves rely on gravity to close the flaps. When the gas flows forward, the flap is pushed away; when the gas stops flowing or attempts to reverse flow, the flap automatically closes due to its own weight. This type of check valve is suitable for low pressure systems.
Solenoid Check Valve
The electromagnetic check valve controls the opening and closing of the flap by the magnetic field generated by the electromagnetic coil. When the coil is energized, the magnetic field sucks the flap and opens the channel; when the coil is de-energized, the flap returns to its original position and closes the channel. This type of check valve has a fast response speed and is suitable for automatic control systems.
Performance parameters of check valve
Maximum working pressure
The maximum working pressure of the check valve refers to the highest gas pressure it can withstand. When selecting a check valve, it is necessary to ensure that its maximum working pressure is higher than the maximum pressure in actual use to ensure safety and reliability.
Flow Range
The flow range refers to the minimum and maximum gas flow that the check valve can handle. The appropriate flow range should be selected according to the actual needs to ensure the smooth operation of the system.
Connection method
Check valve has a variety of connections, including threaded connections, flange connections and quick plug connectors. Choosing the appropriate connection method can simplify the installation process and improve the sealing and stability of the system.
Material Selection
The material of the check valve has a great influence on its performance and life. Commonly used materials include stainless steel, cast iron, plastics and copper alloys. Stainless steel and cast iron are corrosion-resistant, high-strength, and suitable for harsh environments; plastic and copper alloys are lightweight and low-cost, suitable for general use.
Check Valve Selection Guide
Identify application scenarios
First of all, you need to clarify the application scenario of the check valve. Different application scenarios have different requirements for check valves. For example, industrial production may require higher performance check valves, while home repairs can choose more cost-effective products.
Evaluate performance requirements
Next, evaluate specific performance requirements, such as maximum operating pressure, flow range, and connection methods. These parameters will directly affect the applicability and reliability of the check valve.
Cost-effectiveness considerations
Finally, consider cost-effectiveness. Choosing a check valve with excellent performance and reasonable price can reduce the overall input cost while ensuring the performance of the system.
Installation procedure of check valve
Preparations
Before installing the check valve, you need to prepare the necessary tools and materials, such as wrenches, sealants, etc. At the same time, ensure that the work area is clean and easy to operate
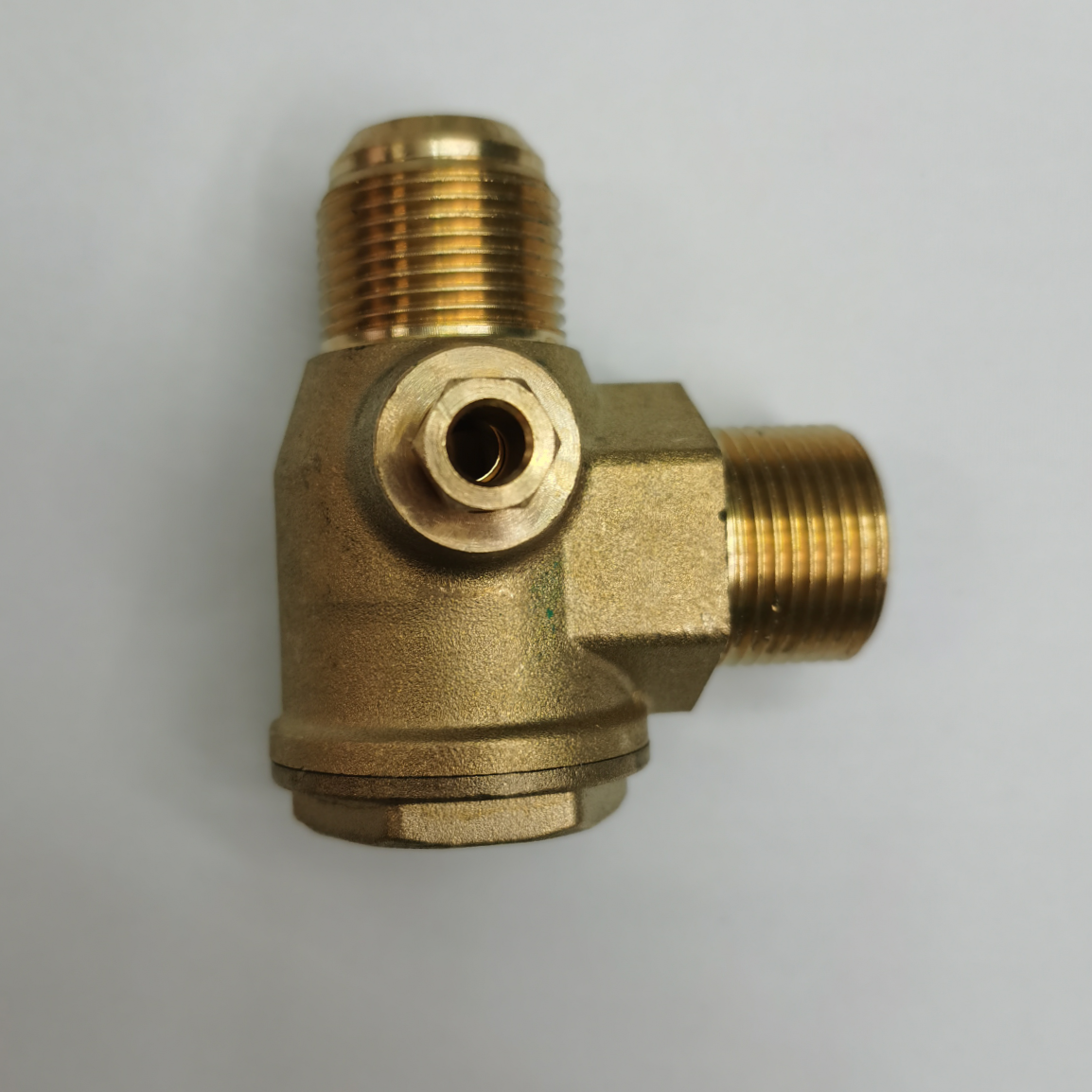