
The role of the check valve: the core guardian of the air compressor system
When we talk about air compressor systems, there is an often overlooked but extremely important component-the check valve. It is like a silent guardian, ensuring that the gas only flows in a single direction, preventing the potential risks posed by countercurrent. This simple and effective design not only helps to protect other sensitive equipment from damage, but also greatly improves the reliability and safety of the entire system.
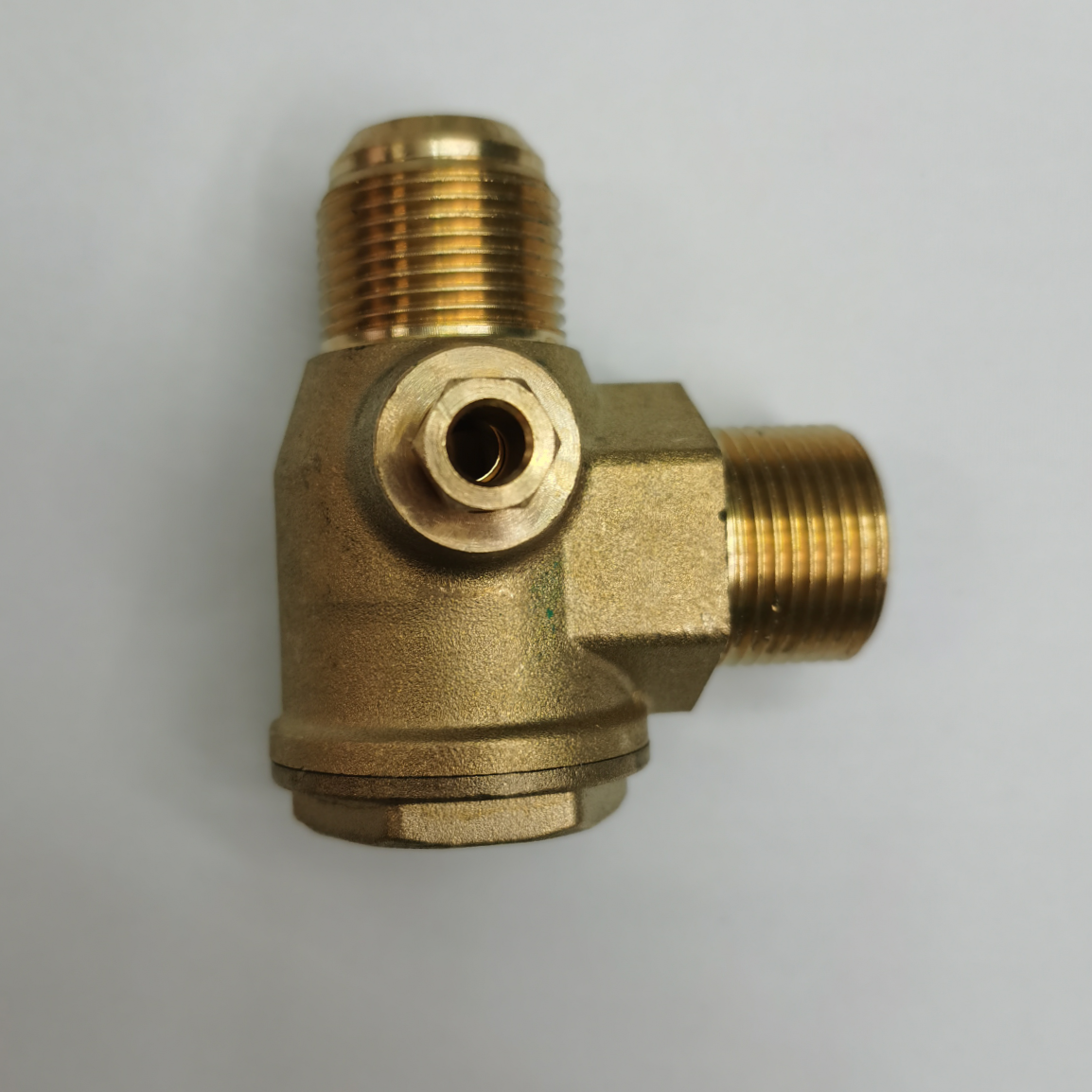
Imagine this scenario: if a working air compressor suddenly encounters a power outage or other emergencies, if the lack of proper check valve configuration, the high-pressure gas stored in the pipeline will instantly flow back to the source, causing a huge impact. This will not only damage the pump body and other components, but may also endanger the personal safety of the operator. In the actual production environment, many factories have faced the risk of frequent maintenance, high cost and delay due to improper selection or poor quality check valves. Thus, the correct installation and selection of the right type of check valve is very important.
In-depth Analysis: Structure and Operation Mechanism of 3/4-inch Check Valve
In order to better understand and use this key component of the check valve, we need to understand its internal structure. From the outside, an ordinary 3/4-inch check valve does not seem to have much special; however, once you disassemble its shell, you will find that it contains precise design and technical details. Each tiny part works together to accomplish a vital mission-to maintain a one-way flow.
The first is the spring. As one of the main sources of adjustment force, it can provide sufficient preload for the spool in the closed state, so that the two are closely combined to form a sealed loop. When there is a positive pressure to push, the valve core will overcome the elastic force to open the channel to allow the gas to pass smoothly; otherwise, the outlet end is tightly closed to prevent any form of reverse movement. This is followed by the valve core itself, which is usually made of high-strength stainless steel, which has excellent wear resistance and can maintain its performance for a long time in harsh environments. Finally, the shell part, in most cases cast iron or brass casting, both durable and can withstand the adverse effects of changes in the external environment.
With these carefully arranged internal components, we can see how much wisdom is behind a seemingly simple mechanical device. By properly matching different material properties and following the laws of physics to arrange the layout, engineers have successfully created a high-efficiency and stable check valve product series.
Hands-on: Easily master the correct installation skills
Now that you understand the importance of check valves and how they work, the next step is to learn how to properly install them into your air compressor system. Don't worry, even new people who are new to this task for the first time don't have to feel difficult. As long as you follow the following instructions step by step, I believe that all steps can be successfully completed soon.
Before you begin, it's obviously essential to have the tools and items you need, such as wrenches, screwdrivers, and other basic equipment. In addition, it is necessary to carefully read the attached product manual to ensure that each link can be strictly implemented in accordance with the specifications provided by the manufacturer. Especially in the connection interface position adjustment stage should be extra careful, remember to tighten the nut evenly, to avoid deviation and lead to problems in the follow-up work.
It is worth noting that the friction resistance between the moving parts can be reduced by applying an appropriate amount of lubricant during the assembly process, which is very useful for ensuring overall stability. It is also a good idea to use a spirit level to check whether the bottom plane is flat, because it can directly affect the stability of the final fixation. Every time a part is completed, it should be immediately reviewed to see if there is any missing unfastened place until the whole process is completed.
the last procedure is a trial run test. only after full inspection and confirmation that there is no abnormal sound or leakage can it be safely put into use. This will not only ensure the maximum benefit of the initial investment, but also allow you to enjoy a carefree service experience for a long time in the future.
Shop Savvy: Pick the 3/4 inch check valve that's right for you
In the face of a wide range of market choices, it is not easy to find the most suitable check valve for your needs. However, as long as you master a few core points, you can quickly narrow the scope of screening until the final selection of satisfactory products. The first is to clarify the maximum pressure level and the expected flow rate corresponding to the specific application, which is the basic condition that determines everything. Secondly, pay attention to the quality of raw materials, especially for those facilities that need to be exposed to the outdoor environment for a long time, metal materials with good corrosion resistance characteristics are particularly important.
In addition to the above two main considerations, cost performance is also a factor that cannot be ignored. Although the low price sounds tempting, it is undoubtedly more than worth the loss if the quality and service quality are sacrificed. On the contrary, excessive pursuit of high-end brands may also lead to unnecessary economic burden increase. So finding a balance is the wisest thing to do. In addition, the perfect after-sales service system is also worthy of attention. After all, no one can predict whether there will be various unexpected situations in the future?
In order to allow consumers to compare various options more intuitively, the following is a comparison table of the advantages and disadvantages of several well-known brands:
Brand name | Advantages | Disadvantages |
---|---|---|
A | Affordable | Weak after-sales |
B | Excellent quality | Relatively expensive |
C Card | Comprehensive service | Long lead time |
I hope this form will provide you with a valuable reference.
Answering questions: solving practical problems you care about
Even with detailed knowledge and support information, you will inevitably encounter some confusing specific situations. To this end, we will collect a series of the most common questions about the 3/4 inch check valve, and give a targeted and easy to implement the answer scheme.
For example, "Why is my new check valve always making so much noise?" The answer is quite simple-it may be due to a resonant effect caused by turbulence caused by excessive dirt accumulation at the air intake. At this time, it is only necessary to thoroughly clean the filter to eliminate the annoying noise. Another problem is "I found that the recent use of low frequency can still occasionally leak", which is likely to be caused by the aging of the gasket leakage phenomenon, timely replacement of new seals can often achieve immediate results.
In order to prevent similar failures from recurring and affecting work efficiency